A Basic Guide To Construction Welding
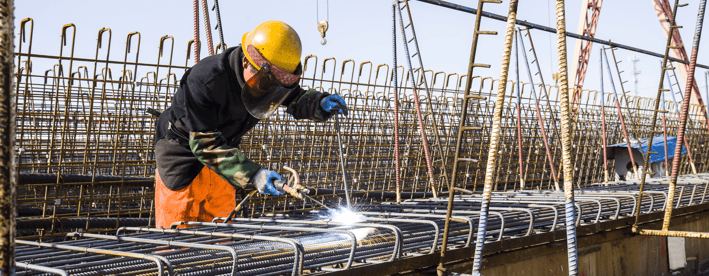
Welding is one of the basic skills that anyone working with metals has. Its primary purpose is to connect two separate objects. In most cases, workers weld thermoplastics and metals, such as steel frames, using filler materials called welding rods. Many find welding an essential process to make buildings or structures more durable. For this purpose, welders employ a variety of techniques.
Since welding has become a must in the fields of manufacturing, automotive, and construction, many people have developed their welding skills. While welding skills are generally necessary to land a job in the mentioned industries, they're even more valuable because welders can do standalone construction projects. This way, they can save money since they don’t have to hire anyone else for the job, and they can customize the design of whatever final product they’re looking to create.
If you’re an aspiring metalworker or welder, it would do you a world of good to learn more about construction welding. Keep reading to accomplish just that.
Common Methods Of Welding
Metalworkers need to know various types of welding so they can apply the appropriate ones to different situations. Generally, fusing metals or thermoplastic materials will need more than one kind of welding. From the preparation to the final touches, here are the most common welding types you should be aware of:
Tack Welding
Welders do a tack weld when they want to hold metals in place. This type only requires soft welding spots as its purpose is to join materials for a short time. Welders should avoid pressing too much to the extent that the welded points become hard to break.
Tack welding is also done to ensure material alignment and strength. However, in the first place, welders should consider the quality and type of the metals they’re using. These attributes affect how durable the connection is and how many welded spots are necessary during the process.
Shielded Metal Arc Welding
This process is also referred to as stick welding. Just like in tack welding, a stick or rod is utilized in joining materials through this method. But in this case, workers use an electrode flux-coated metal rod and the component to be welded. The melting of the rod and the workpiece creates a weld.
Gas Tungsten Arc Welding
For this, the worker uses an electric arc. Metals are welded with a tungsten-based electrode instead of the usual metal stick. During the process, workers may or may not use a filler material. Since tungsten doesn’t burn off or dissolve, gas tungsten arc welding is preferred by those who work in aero and auto shops.
Gas Metal Arc Welding
Gas metal arc welding uses a shielding gas and an electrode to fuse components together. Apart from that, this type of welding is known to protect workpieces from contamination. Many welders use this method in joining aluminum and steel in cars.
Flux-Cored Arc Welding
This is often used for thick and heavy metals, and it involves a constantly fed and flux-filled hollow tube. Like the two previous welding methods mentioned, this type welds an electrode and the parent materials.
How Construction Welding Works
Welding Preparation
Before welding, workers need to make certain that the metals are free from rust, grime, and grease, especially the portions to be attached. In most cases, welders clean the pieces with cotton cloths or high-pressure washers if the dirt has developed into hardened grime and rust.
Wearing Protective Gear
Welders need to keep themselves safe during welding processes such as brazing, connecting, and cutting of metals. In those situations, workers become prone to radiation, sparks, fumes, and other welding hazards. Such factors may cause eye damage and burns. In some cases, workers could even be electrocuted.
To prevent accidents from happening, welders could opt to wear personal protective equipment (PPE), helmets, and, most importantly, safety goggles.
Setting Up The Workpiece And The Workspace
Workers often set up a platform for welding. However, they should make sure that their workspace is safe and clean to avoid injuries and other problems. A scheduled cleanup should be done prior to starting or continuing a project.
Proper Rod Movement And Positioning
Place the rods at a slanted angle—roughly 15 degrees from the vertical. The rod has to move in a straight direction. In addition, the arc length should neither be too long nor too short.
Hitting The Arc
Welders could either scratch or tap with the base material’s end and the electrode’s end. The time spent scratching and tapping depends on how deep or attached the welder wants the metal pieces to be. In other words, the stronger the bond of the metals, the longer the welder should scratch or tap.
Creating A Good Weld
The quality of welding dictates the material and bond strength of the joined metals. In most cases, good welds have the following attributes:
- Uniform
- Often welded in a straight direction
- Doesn’t crack in the middle
- Completely fused
- Well-feathered into the parent material
- Has even ripples
For better results, welders refine their welds and beads by removing slags and other poorly welded parts.
Cleaning The Workpiece And Workspace
Cleaning should always be a part of the welding process. It reduces the chances of post-work injury and other troubles. Typically, workers or a team of cleaners use homemade cleaning solutions such as baking soda for slags and flour and peroxide for burnt marks. For the finished workpiece, wire brushing is the typical cleaning method used.
Wrapping Up
Without welding, erecting strong structures wouldn’t be possible. Welding properly is necessary to permanently connect separate materials. It results in a durable bond, a flawless seam, and an efficient structure. For this reason, many are seeking to at least learn the basics of construction welding. When a person acquires that particular skill, they can work with various contractors to build everything from homes to skyscrapers.
If you really want to be an excellent welder, you may start learning the fundamentals with the help of articles such as this before getting enough experience and perhaps even earning a welding certification. Afterward, you can put your skills to good use by becoming part of the construction industry and helping meet the demand for all types of buildings.
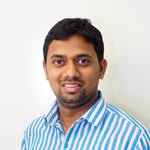
Ravindra Ambegaonkar
Ravindra, the Marketing Manager at NY Engineers, holds an MBA from Staffordshire University and has helped us grow as a leading MEP engineering firm in the USA
Join 15,000+ Fellow Architects and Contractors
Get expert engineering tips straight to your inbox. Subscribe to the NY Engineers Blog below.