Improving HVAC Efficiency in Commercial Buildings with Variable Frequency Drives
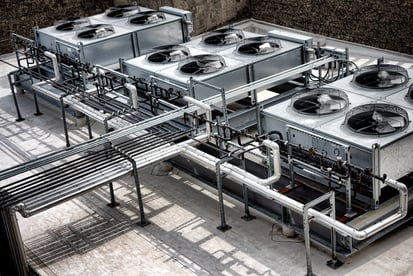
HVAC systems come in various configurations that differ significantly from each other. For example, an air conditioning system based on packaged rooftop units is drastically different from a chiller plant. However, HVAC installations have a common denominator: they use electric motors that are subject to variable loads. Regardless of whether these motors are used to drive compressors, water pumps or fans, there is a great opportunity to save energy by optimizing part-load operation.
In general, running a motor at partial speed is more energy-efficient than running it intermittently at full speed.
- Intermittent operation only provides linear savings. For example, a cooling tower fan with a duty cycle of 80% consumes 20% less energy than an identical fan operating full-time.
- Reducing motor speed provides cubic savings.. On the other hand, slowing down a fan to 80% speed reduces energy consumption by nearly 50%. The average airflow is the same as that of a fan running at full power 80% of the time, but savings are boosted significantly thanks to speed control.
Speed control can be accomplished with variable-frequency drives (VFD), and they have a broad range of applications in HVAC systems due to the cyclic nature of loads. It is important to note that VFDs are also known as variable-speed drives (VSD), adjustable-frequency drives (AFD) or adjustable-speed drives (ASD).
Fractional horsepower motors in small-scale HVAC systems can also achieve significant savings with speed control. The main difference here is that electronically commutated motors (ECMs) are more cost-effective than VFDs in these applications.
Green engineering shows promise for improving energy efficiency and renewable power generation in the near future.
See where green engineering is expected to be within the next year.
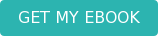
How Does Variable Frequency Drive Work
As explained by electrical engineering textbooks, the speed of an electric motor is defined by the power supply frequency and its internal construction. For example, a motor running at 1800 RPM with the 60 Hz USA power supply would run at 1500 RPM in the UK, where the frequency is 50 Hz. Thus, if a motor is suitable for operation at reduced frequency, its speed can be ramped down during part load conditions to achieve energy savings. VFDs are connected between the power supply and the motor, adjusting voltage and frequency as a means of speed control.
In applications where only single-phase power is available, VFDs can be used to integrate three-phase motors while achieving the energy efficiency benefits: there are models capable of producing a three-phase voltage from a single-phase input, while adjusting magnitude and frequency to control motor speed.
In addition to improving energy efficiency, VFDs allow motors to be soft-started by gradually ramping up the voltage and frequency, as opposed to directly applying full voltage at 60 Hz. Electric motors draw from five to eight times their rated current when started directly, and the voltage drop that results from the inrush current may damage sensitive equipment.
The main limitation of VFDs is that they produce a phenomenon called harmonic distortion, where high-frequency currents are induced in branch circuits. However, this can be controlled with a properly-specified harmonic filter; this device absorbs current distortions at the point of consumption, preventing their propagation throughout the installation.
VFD Applications in HVAC Systems
In most cases, VFDs are deployed in HVAC systems to control the speed of blower fans, pumps or compressors.
Cooling Tower Fans
The main purpose of a cooling tower is removing the heat from a water circuit, which may be used in turn for process cooling or for a chiller plant. Cooling towers use fans to establish an airflow, improving heat removal through convection. These are open discharge fans, where there is no ductwork creating resistance to airflow; hence, the savings opportunity through speed control is significant.
When a VFD is deployed for a cooling tower fan, speed is normally controlled based on water temperature. Rather than cycling the fan on and off, it can be driven at reduced speed so that the water returning to the chiller or process is kept at a constant temperature – as previously explained, reduced-speed operation is far more efficient than intermittent operation at full speed.
Air-Handling Units and Packaged Rooftop Units
Unlike the fans in cooling towers, those used in AHUs and packaged RTUs blow air into a duct system, which offers higher resistance and requires a specific static pressure and airflow to be established. These ducts may have several outlets with variable-air-volume (VAV) boxes, where airflow is controlled individually for each zone with a damper.
Without a VFD, the blower fan in the AHU or RTU operates at full speed, and each VAV box is adjusted individually. This is an inefficient approach, however – if neither of the VAV boxes is fully open, energy is being wasted in the form of extra pressure. On the other hand, if the blower is equipped with a VFD, an interesting energy-saving strategy becomes possible:
- Blower speed can be gradually reduced while VAV boxes are opened incrementally, to keep the airflow and temperature constant.
- The temperature of different zones is unaffected but pressure is reduced, saving energy.
- Speed reduction continues until one of the VAV boxes reaches the fully open position. At this point it is not possible to reduce speed further without affecting indoor temperatures.
There is also a comfort benefit with this control strategy: the reduced pressure drop translates into less noise, making indoor environments more comfortable.
Speed Control for Water Pumps
Water circuits are a key element of many HVAC installations, including those that use chillers, boilers and water-source heat pumps. Since HVAC loads are variable, it is often necessary to adjust the water flow depending on total system load. There are three main ways to achieve this:
- Choke Valve-A choke valve is installed in line with the flow, and as implied by its name it regulates flow by closing partially. This control method is simple, but the resulting pressure loss represents a considerable waste of energy.
- Recirculation Valve-With this approach a valve is installed on a parallel recirculation circuit, and it is opened gradually to divert a part of the water flow, reducing the flow in the main circuit. In this case, however, there is also a significant energy loss because the recirculated water represents pumping power.
- Pump Speed Control– The most energy efficient approach is to install a VFD on the pump motor. If a reduced water flow is required, it is just a matter of reducing the pump speed accordingly. With no pressure or recirculation losses, the savings achieved are significant. This setup also uses a choke valve for convenience, but it is normally kept in the fully open position, since the VFD regulates flow.
Chillers with Variable-Speed Compressors
In chilled water air conditioning systems, the chiller is by far the piece of equipment with the highest energy consumption. Therefore, installing the most efficient chiller model that can be afforded is highly recommended.
Energy efficient chillers have helical rotary compressors, capable of adjusting their speed with a VFD, depending on cooling needs. Some models may feature multiple individual compressors to achieve enhanced flexibility and increased part-load efficiency.
When a chiller is highly efficient, the control strategy is normally based on maximizing its capacity rather than running it at the lowest possible set point. The savings achieved by reducing the load on complementary systems tend to be far greater than the extra consumption at the chiller. There are exceptions, of course, and only monitoring and control can offer the correct answer 100% of the time.
Integrating the Entire HVAC System
Equipping all motors in an HVAC system with VFDs is a first step towards energy efficiency, but the best results can only be achieved with central control system, capable of assessing building conditions and adjusting HVAC set points in real time.
The interaction between a chiller and a cooling tower is a great example of how control engineering and VFDs can be applied to HVAC installations:
- Reducing the cooling tower fan speed increases the cooling load on the chiller.
- The reverse also applies: reducing refrigeration power at the chiller may require more heat to be rejected by the cooling tower.
If the chiller has a high efficiency, the best option in most scenarios is reducing the cooling tower load. However, only a control system can balance the operation of both components in real time. Ideally, the control system should be able to determine the set point for each individual VFD so that power consumption is minimized at the total system level.
Of course, the performance of an HVAC system starts from the design phase. For optimal results, make sure you work with licensed and qualified professionals. Installing an efficient and automated HVAC system from the start is much less expensive than upgrading an existing installation.
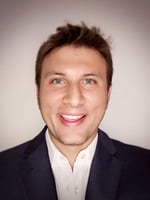
Michael Tobias
Michael Tobias, the Founding Principal of NY Engineers, currently leads a team of 150+ MEP/FP engineers and has led over 4,000 projects in the US
Join 15,000+ Fellow Architects and Contractors
Get expert engineering tips straight to your inbox. Subscribe to the NY Engineers Blog below.