Overcoming the Challenges in Retrofitting MEP Systems in Existing Buildings
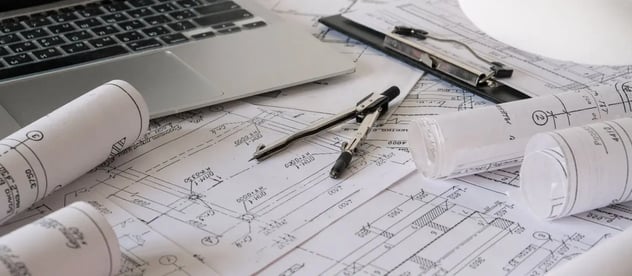
Retrofitting a building involves changing its systems or structure after its initial construction and occupation. This work can improve amenities for the building's occupants and improve the performance of the building. As technology develops, building retrofits can significantly reduce energy and water usage.
Retrofitting MEP systems in older buildings is challenging due to space constraints, outdated materials, and evolving codes. Yet, these upgrades are essential for improving energy efficiency, enhancing safety, and extending the building's lifespan. Despite complexities, modernizing MEP infrastructure is crucial for long-term sustainability.
As per Utility Dive news Buildings are responsible for 37% of global emissions, and the U.S. needs to triple its retrofit rate to meet net-zero targets.
The Need for Retrofitting MEP Systems
- Increased Energy Efficiency: Upgrading to energy-efficient HVAC, electrical, and plumbing systems can significantly lower utility costs, helping building owners reduce monthly energy bills and achieve long-term savings.
- Enhanced Safety: Outdated electrical and plumbing systems can lead to fire risks, leaks, or contamination. Retrofitting with modern systems enhances building safety and security.
- Compliance with Modern Codes: Building codes evolve to enhance safety, efficiency, and sustainability. Retrofitting ensures older buildings meet current standards, protecting occupants and avoiding legal risks.
- Improved Building Performance: Upgrading MEP systems enhances building performance by boosting comfort, functionality, and durability. Modern HVAC and plumbing systems improve climate control and ensure reliable water supply and drainage.
Key Challenges and Solutions in Retrofitting MEP Systems
1. Outdated and Incompatible Infrastructure
Challenge:
Older buildings often have outdated infrastructure that is incompatible with modern MEP systems. Electrical wiring, plumbing, and HVAC components may be too old or deteriorated for new equipment. Additionally, many buildings still use outdated gas-fired boilers for space heating, which aren't compatible with new systems.
Solution:
The first step is to assess the infrastructure thoroughly. Inspect electrical wiring, plumbing, and HVAC to identify needed upgrades. Replace old plumbing with corrosion-resistant materials like copper or PEX, following code requirements. Ensure electrical systems comply with current safety standards to prevent fires or failures. Consider upgrading to electric heat pumps for a modern, energy-efficient alternative to gas boilers.
2. Limited space for equipment and Ductwork
Challenge:
Older buildings often have cramped spaces, making it difficult to install or upgrade modern MEP systems. This is especially challenging for HVAC systems, which require bulky equipment such as air handling units, chillers, and ductwork.
Solution:
Engage experienced MEP engineers who have the expertize to design efficient solutions that maximize the use of available space. This might involve utilizing compact equipment, exploring alternative duct routing options, or even considering modular or prefabricated systems that can be assembled on-site.
3. Maintaining Code Compliance
Challenge:
New installations must comply with modern building codes and regulations related to energy efficiency, water conservation, fire safety, and electrical systems. These codes are continuously updated, and older buildings often fall far short of meeting these standards.
Solution:
Work closely with regulatory authorities and building officials to understand and navigate applicable codes and permitting processes. Engage MEP professionals with expertise in code compliance to ensure that retrofit designs meet all regulatory requirements and standards.
4. Budgetary Constraints
Challenge:
Retrofitting MEP systems can be expensive, particularly when unexpected challenges emerge or when upgrading to energy-efficient equipment.
Solution:
New York offers several incentives to encourage building retrofits aimed at improving energy efficiency and reducing emissions. Some of the incentives providers are New York State Energy Research and Development Authority (NYSERDA), Con Edison and PSEG.
Conduct a detailed cost-benefit analysis to identify areas where savings can be achieved without sacrificing long-term efficiency. For example, investing in high-efficiency HVAC systems may have a higher upfront cost but can lead to significant energy savings over time. Additionally, phased implementation can spread costs over a longer period, easing budgetary constraints.
Energy-efficient retrofitting upgrades qualify for tax deductions under Internal Revenue Code (IRC) Section 179D. This can further offset the initial costs of upgrading, making it a more attractive option for building owners.
The maximum deduction amount allowed each year per sqft. of property area is as follows:
Tax Year | Maximum Full Amount Allowed ($/sqft) | Maximum Partial Amount Allowed ($/sqft) |
---|---|---|
All years beginning before January 1, 2021 | $1.80 | $0.60 |
For tax years beginning on or after January 1, 2021 | $1.82 | $0.61 |
For tax years beginning on or after January 1, 2022 | $1.88 | $0.63 |
Maximum Amount Allowed—Line 1(d)* checked | Maximum Amount Allowed—Line 1(d)* not checked | |
For tax years beginning on or after January 1, 2023 | $5.36 | $1.07 |
For tax years beginning on or after January 1, 2024 | $5.65 | $1.13 |
Source- Internal Revenue Service(IRS)
Note-
* Line 1, Column (d) - Laborers and mechanics employed in the installation of Energy efficiency property are paid wages at rates not less than the prevailing rates for construction.
As per Fortune Business Insights, The global energy retrofit systems market size is projected to grow from USD 182.99 billion in 2024 to USD 234.96 billion by 2032.
5. Minimizing Disruption to Occupants
Challenge:
Many retrofitting projects occur in occupied buildings, which adds another layer of complexity. Disrupting tenants, employees, or customers during the retrofit process can lead to lost revenue or complaints.
Solution:
Consider conducting retrofit activities during off-peak hours, weekends, or holidays to minimize disruptions, and keep occupants informed with regular updates on construction timelines. Clear communication helps reduce inconvenience and strengthens relationships with building occupants.
Conclusion
Retrofitting MEP systems in existing structures is a complex and multifaceted process, requiring a deep understanding of both the building’s limitations and modern engineering solutions. NY Engineers, a leading MEP design firm, brings a wealth of experience to retrofitting projects, offering innovative solutions that address these complexities. Whether it’s integrating high-efficiency systems in a historic building or ensuring minimal disruption during an upgrade, we deliver results that improve energy efficiency, enhance safety, and ensure long-term compliance with building codes.
Are you ready to transform your building with cutting-edge MEP solutions? Reach out to NY Engineers today and discover how we can help you achieve your retrofit goals.
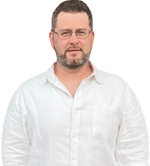
Keith Fink
Keith is the Franchise Brand Manager at NY Engineers, Keith is all things related to our project portfolio, brands and all things you need to know before we start your project.
Join 15,000+ Fellow Architects and Contractors
Get expert engineering tips straight to your inbox. Subscribe to the NY Engineers Blog below.