Space Cooling: Types of Compressors Used in Chillers
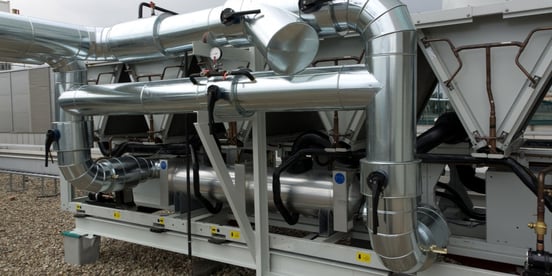
The compressor performs a fundamental role in the operation of a chiller, making it possible to remove heat from indoor spaces or from industrial processes. Once the refrigerant in a chiller absorbs the heat from a building or process it becomes a gas, but it is incapable of releasing the heat right away in this form. However, after the compressor raises the pressure and temperature of the gasified refrigerant, the heat can be expelled. Air-cooled chillers release heat directly outdoors, while water-cooled chillers release it into a stream of water that is then pumped to a cooling tower.
There are many types of compressors, each with advantages and disadvantages. This article will provide an overview of the three types most commonly used in large commercial chillers. HVAC engineers can determine the best option for your building based on load characteristics.
- Reciprocating compressor
- Centrifugal compressor
- Rotary-screw compressor
In commercial space cooling systems, the compressor is typically the component with the highest electricity consumption. Therefore, it is important to have a well-sized unit, and of a type that is suitable for the application at hand.
Improve the performance of your space cooling systems.
Reciprocating Compressors
The reciprocating compressor has a shape similar to that of a car engine cylinder, and it is also known as piston compressor for this reason. Refrigerant that has evaporated after absorbing heat is fed into the cylinder through suction valves, and compressed by the piston before being sent to the condenser. Reciprocating compressors can be classified into two subtypes, based on their construction:
RECIPROCATING COMPRESSOR SUB-TYPE |
DESCRIPTION |
Hermetically sealed |
The compressor and the motor driving it are coupled directly and they share a sealed housing. |
Open |
The compressor and the motor have separate housings. In general, this configuration has a higher efficiency and a longer service life, while having simpler maintenance needs. |
For a given cooling capacity, reciprocating compressors have a lower upfront cost than centrifugal and rotary-screw compressors. They also offer design flexibility, allowing multiple units to be installed together to serve variable cooling loads - individual units are activated or deactivated as needed.
The main limitations of reciprocating compressors are their lower energy efficiency and their demanding maintenance, compared with other types of compressors. Also, although these compressors can achieve good capacity control when multiple units are used, there are few options to modulate the capacity of an individual unit. The two most common options are:
- ON/OFF Control: Operating the unit intermittently (reduced duty cycle) when its full capacity is not required.
- Cylinder Unloading: The compressor cylinder can be equipped with additional suction valves or a clearance valve. These valves remain closed when the unit operates at 100% capacity, but may be opened in several combinations to achieve reduced capacity.
Centrifugal Compressors
If a reciprocating compressor can be compared to a car engine, this type is comparable to a water pump because it also uses an impeller, with the difference that it operates with refrigerant. These compressors are also available in hermetic and open models, where the open construction offers higher efficiency.
At rated load, centrifugal compressors are more efficient than both reciprocating and rotary-screw compressors. They also offer a compact construction and are available in a wide range of cooling capacities. Capacity control is normally achieved with inlet vanes that increase or decrease the flow of refrigerant into the impeller.
Despite their superior efficiency at full load, centrifugal compressors suffer from a drastic loss of efficiency at part-load. At very low cooling loads they are rendered unable to operate, due to a phenomenon called surging: refrigerant that is already compressed flows back into the impeller, disrupting its operation.
Centrifugal compressors have the least number of moving parts among the three main compressor types, which means there are less components to service. However, in most cases the impeller must be factory-ordered if fails; suppliers rarely keep stock because it’s a highly specialized component. Balancing and vibration must also be checked frequently to avoid loss of performance and premature component failure.
Rotary-Screw Compressors
This type of compressor uses two helical screws that are designed to mesh with one another seamlessly while rotating at high speed. They are manufactured with high precision to create a clearance between them, which serves as the compression chamber. These compressors are available in hermetic and open versions like the two previous types described, and capacity control is achieved with a special valve that varies the internal volume ratio.
Although centrifugal compressors are more efficient at full load, rotary-screw compressors offer the best performance during part-load operation. Since the cooling load on a building varies throughout the year, rotary-screw compressors tend to achieve the lowest operating cost overall, even if centrifugal compressors are more efficient at full load.
The main limiting factor of rotary-screw compressors is their high price. If the application does not provide opportunities to take advantage of their capacity control and their superior part-load efficiency, another type of compressor can be considered.
Comparing the Three Types of Compressors
The following table compares the three compressor types described above, based on many key metrics such as initial investment and maintenance complexity.
COMPRESSOR CHARACTERISTICS |
RECIPROCATING |
CENTRIFUGAL |
ROTARY-SCREW |
Initial investment |
Lowest |
Intermediate |
Highest |
Energy consumption per ton of refrigeration (at full load) |
Highest |
Lowest |
Intermediate |
Part-load performance |
Good |
Poor |
Best |
Maintenance |
Has the highest number of moving parts, is subject to constant wear and requires frequent part replacements. |
Has the least number of moving parts, but it is important to monitor the unit for balance and vibration issues, due to the high rotating speed. |
Has an intermediate number of moving parts, but balance and vibration issues are less common than in centrifugal compressors. This compressor type is the least demanding in maintenance requirements. |
High-rise commercial buildings, like those found in New York City, can generally achieve the best results with a space cooling chiller that uses a rotary-screw compressor. Despite being the most expensive option, it offers the best performance under the variable cooling load that characterizes buildings, while being the simplest system to service - consider that maintenance activities can be quite disruptive in a busy commercial property in NYC.
Working with qualified HVAC design engineers ensures that your property gets a space cooling system that delivers high performance at an optimal energy cost. Chiller selection is a key element, but it is also important to specify adequate complementary systems: air handling units, hydronic piping, cooling towers, HVAC controls, etc.
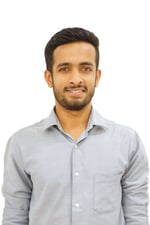
Sanket Abhang
Sanket Abhang is a Plumbing and Fire Protection Design Engineer who holds a Mechanical Engineering Degree from the University of Mumbai, India. Recent projects include Community Access, Jackson Avenue, 330 Grand Street and many private residences & commercial kitchens.
Related Posts
Join 15,000+ Fellow Architects and Contractors
Get expert engineering tips straight to your inbox. Subscribe to the NY Engineers Blog below.