The Advantages of Using Pneumatic Cylinders in Industrial Applications
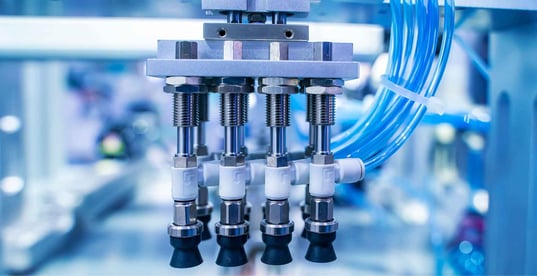
In the realm of industrial automation, efficiency and reliability are paramount. One technology that has proven its mettle time and again is the use of pneumatic cylinders. These versatile mechanical devices, also known as air cylinders, harness the power of compressed air to produce a reciprocating motion, making them invaluable in a wide array of industrial applications. In this blog post, we'll explore the numerous advantages of employing pneumatic cylinders and why they continue to be a preferred choice in the world of manufacturing and automation.
The Power of Pneumatic Cylinders
Pneumatic cylinders are workhorses of the industrial world, and for good reason. Here are some of the key advantages they offer:
1. Speed and Precision
Pneumatic cylinders excel at providing rapid and precise motion control. Whether it's moving a conveyor belt, controlling a robotic arm, or operating a packaging machine, these cylinders offer exceptional speed and accuracy. This enables manufacturers to optimize their production processes, leading to higher throughput and improved product quality.
2. Cost-Efficiency
Compressed air, the driving force behind pneumatic cylinders, is often readily available in industrial settings. This makes pneumatic systems cost-effective to implement and operate. Unlike some alternatives, pneumatic systems require minimal infrastructure and are relatively easy to maintain, translating into lower overall costs.
3. Safety and Reliability
Safety is a paramount concern in industrial environments. Pneumatic systems are inherently safer than some other power sources, such as electricity or hydraulics, as they do not pose the same risk of electrical shock or fluid leakage. Additionally, pneumatic cylinders are known for their reliability, with a long service life and minimal downtime, which is crucial for maintaining productivity.
4. Versatility
One of the standout features of pneumatic cylinders is their adaptability to a diverse range of industrial tasks. Manufacturers can choose from a wide variety of pneumatic cylinders, including compact cylinders, ISO standard cylinders, NFPA interchangeable cylinders, rotary cylinders, rodless cylinders, and even specialty made-to-order units. This versatility allows them to tailor their automation solutions to suit specific applications.
5. Simple Integration
Integrating pneumatic cylinders into existing industrial setups is typically straightforward. Their simplicity of design and standardized interfaces make installation and maintenance relatively hassle-free. This means that manufacturers can quickly implement pneumatic systems without significant downtime or costly modifications.
6. Energy Efficiency
In an era where energy conservation is a top priority, pneumatic systems shine. They are inherently energy-efficient since they only consume compressed air when in use, allowing for precise control of energy consumption. Furthermore, modern pneumatic components are designed with energy-saving features that reduce air consumption, making them an eco-friendly choice.
7. Clean and Contamination-Free
Pneumatic systems are ideal for industries where cleanliness and contamination control are critical, such as food processing and pharmaceuticals. Since they rely on compressed air, there is no risk of hydraulic fluid contamination. This ensures that products remain uncontaminated and safe for consumption.
Harnessing Pneumatic Cylinders
The diverse range of pneumatic cylinders available in the market is a testament to their adaptability. Manufacturers can select the perfect type of cylinder to suit their specific needs. For instance, compact cylinders are excellent for applications with limited space, while NFPA interchangeable cylinders adhere to industry standards, ensuring compatibility and ease of replacement. Rotary cylinders, on the other hand, enable rotational motion, making them indispensable in tasks like indexing and rotary actuation. Rodless cylinders offer a unique design that eliminates the need for an external rod, enhancing space efficiency. When standard options don't quite fit the bill, specialty made-to-order cylinders can be crafted to meet the most unique and challenging requirements.
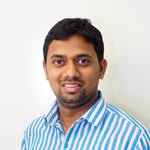
Ravindra Ambegaonkar
Ravindra, the Marketing Manager at NY Engineers, holds an MBA from Staffordshire University and has helped us grow as a leading MEP engineering firm in the USA
Join 15,000+ Fellow Architects and Contractors
Get expert engineering tips straight to your inbox. Subscribe to the NY Engineers Blog below.