Chiller Plants
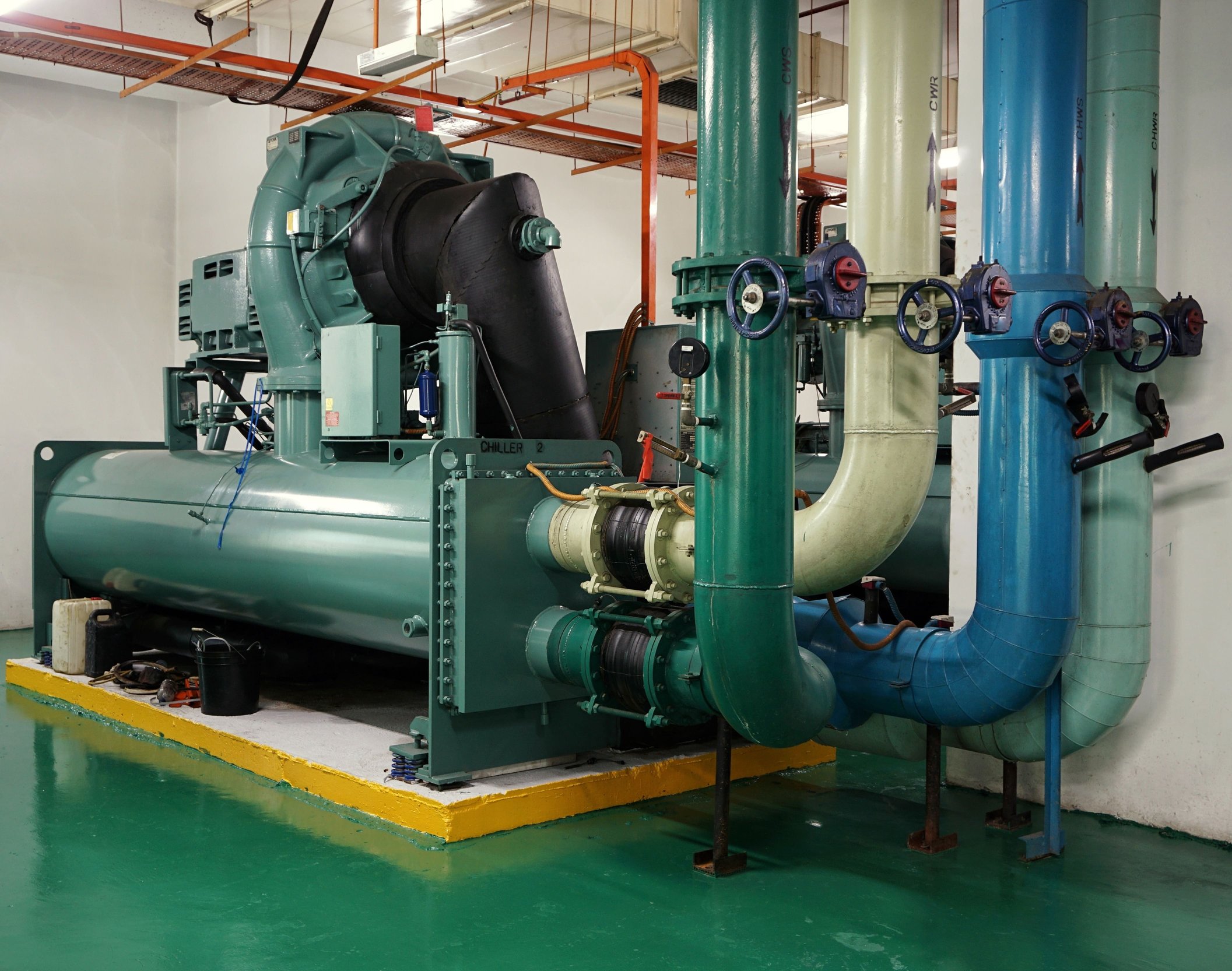
Chiller plants are commonly used for air conditioning in large commercial and industrial facilities. In manufacturing applications, they also play an important role in process cooling. Chiller plants offer a high cooling output and have a much higher efficiency than unitary air conditioners.
Due to their large scale, chiller plants involve a significant upfront investment. Therefore, it is important to make sure they are properly designed.
When deploying chiller plants, the best recommendation is implementing energy efficiency from the start. Upgrading an existing installation is more complex than simply installing a top-performance chiller plant from the start, and you can achieve significant cooling savings.
How Do Chiller Plants Work?
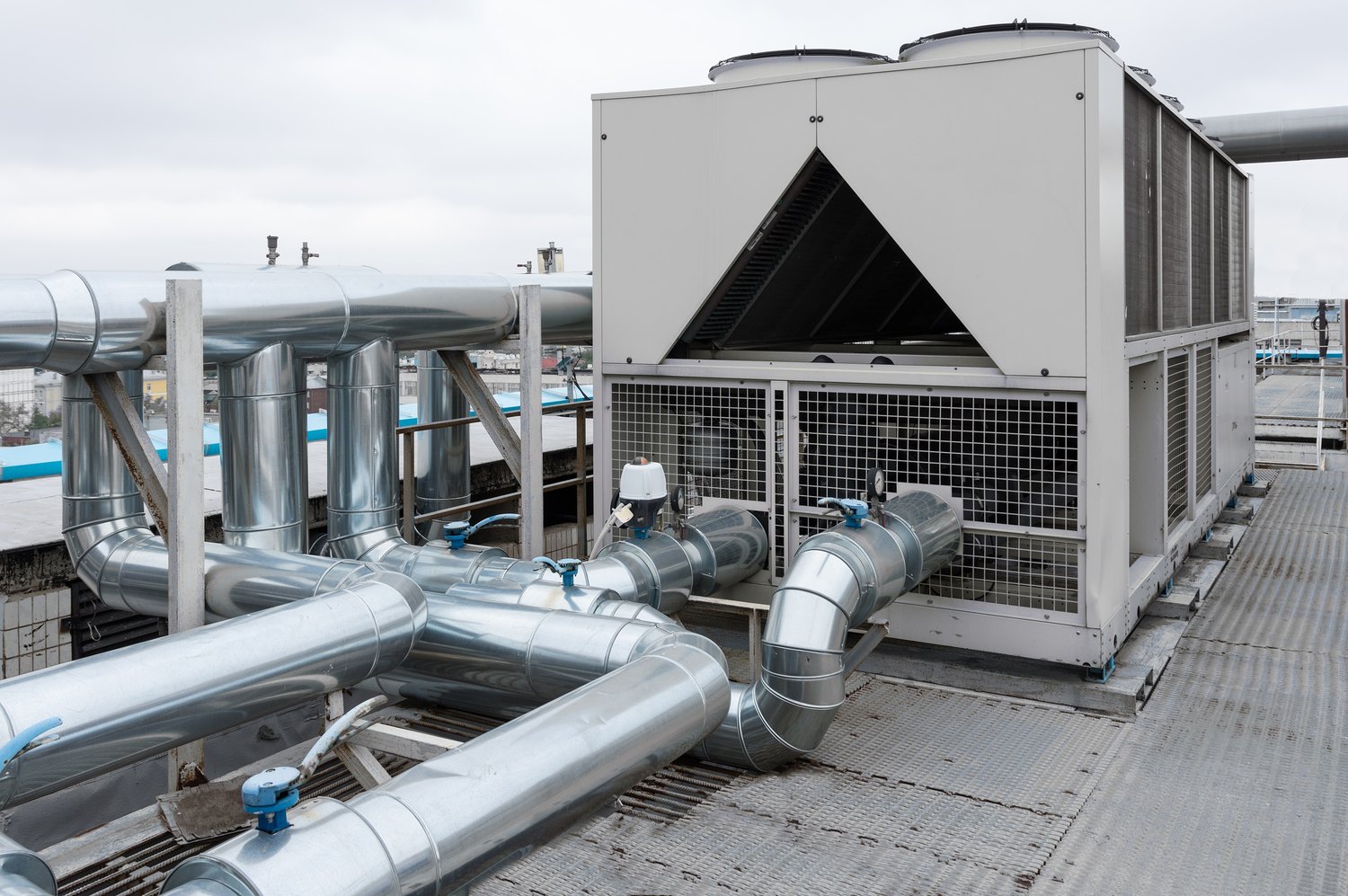
Instead of cooling the air directly, chiller plants use cool water to remove heat from indoor spaces. In simple terms, chillers are larger versions of air conditioning condensers, with cooling capacities often reaching several hundred tons of refrigeration.
- As mentioned above, chiller plants cool large amounts of water instead of cooling the air directly.
- A pumping system distributes chilled water throughout the building, and the piping used for this purpose is called hydronic piping.
- Chilled water is delivered to cooling coils in air-handling units, where fans blow air through the coil to reduce its temperature.
- Air handlers distribute cooled air throughout indoor spaces.
- The temperature of chilled water increases as it captures building heat, and it returns to the chiller plant to be cooled again.
Hydronic piping requires less space than air ducts, since water can hold more heat than air in a given volume. As a result, a chiller plant design can achieve significant space savings in a large building. Pumping water to upper floors is also easier than blowing cool air vertically, which makes chiller plants an excellent option for high-rise constructions.
There is a wide range of chiller plant configurations available, where the common feature is that all use chilled water to remove heat from a building. Chiller plants are typically described based on the compressors they use, and how they release building heat outdoors.
Air-Cooled and Water-Cooled Chiller Plants
All chiller types use water to remove heat from buildings, but they differ in the method used to release the heat outdoors. There are both air-cooled and water-cooled chillers.
- Air-cooled chillers are exposed directly to outdoor air, just like the condenser units of smaller air conditioning systems. A fan is used to establish airflow through the chiller, and the condenser is constantly releasing heat outdoors.
- Water-cooled chillers are not in contact with outdoor air, and instead they use a secondary water loop reject heat. This water loop connects to an outdoor cooling tower where heat is released, and water is then returned to the chiller to remove more heat.
Air-cooled chillers have a simpler configuration because they are only connected to one hydronic piping circuit, while water-cooled chillers use another loop to reject their own heat. However, water-cooled chillers typically offer a higher efficiency than their air-cooled counterparts.
Compressor Types Used by Chiller Plants
Compressors are the core components of chiller plants, since they cool the circulating water used to remove heat from buildings. Most chiller compressors can be classified as reciprocating, centrifugal or rotary-screw types.
Reciprocating compressors use pistons to compress refrigerant, resembling a car engine. Depending on how the chiller is designed, the compressor and its motor may share the same housing, or they can have separate housings.
- Reciprocating compressors are the most affordable, and you can use multiple units together to serve variable loads.
- However, reciprocating compressors are held back by their low efficiency, and their piston mechanisms are demanding in terms of maintenance.
Centrifugal compressors are similar to centrifugal pumps, since a rotating impeller is used to increase pressure. Their cooling output is controlled with inlet valves that regulate the flow of refrigerant in to the compressor.
- Centrifugal compressors are the most efficient type when operating at rated capacity. They are also very compact, and available in a wide range of sizes.
- The main disadvantage of centrifugal compressors is their sharp drop in efficiency when operating under part-load conditions.
Rotary-screw compressors have two matching helical screws that rotate at high speed, and refrigerant is compressed in the space between them. The cooling output is controlled with a special valve that adjusts the volume ratio.
- Although a centrifugal compressor is more efficient at full load, rotary-screw compressors offer the highest efficiency under part-load conditions. Since buildings do not require the full cooling output all the time, these compressors normally have the lowest running costs.
- The main disadvantage of rotary-screw compressors is their higher price, compared with reciprocating and centrifugal units of the same capacity. They are only recommended in applications that benefit from their high efficiency at part load.
Depending on the application, the best compressor option for your chiller plant may vary. For example, if your chiller plant operates at full load most of the time, a centrifugal compressor offers the highest efficiency. The best recommendation is getting a technical assistance from professional HVAC engineers, since they can specify the optimal chiller plant configuration for your building.
Chiller Plants with Ice Storage Tanks
Chiller plants can be equipped with ice storage tanks to improve their energy performance. Commercial and industrial energy consumers are normally subject to capacity charges, where they pay for the highest power demand peak measured in a billing period, in addition to paying a normal tariff for kilowatt-hour consumption.
- If a chiller plant includes ice storage, you can deactivate the compressor when your building’s power demand is high, using stored ice for space cooling.
- This reduces the net power consumption measured by the utility company, leading to a reduction of capacity charges.
Chiller plants with ice storage can also achieve synergy with renewable energy systems. For example, if you have a photovoltaic array or a wind turbine, you can use surplus generation to store ice at the chiller plant. This is often a better alternative than exporting surplus power to the local power grid, since many utility companies only give partial credit for surplus generation.