Green Engineering Tips: How to Convert a Boiler from Oil to Natural Gas
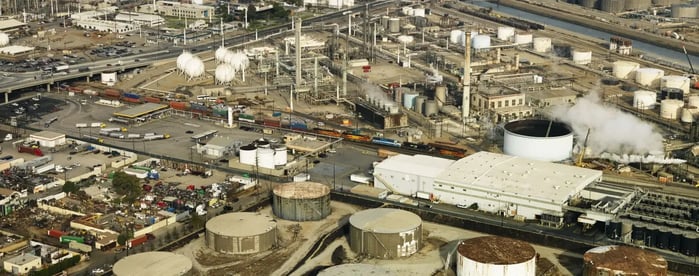
If you're looking for ways to reduce your carbon footprint and save money, converting your boiler system from oil to natural gas is a great green engineering practice. Boiler systems that utilize oil as a means of heating are quickly becoming outdated and environmentally hazardous since they are among the top contributors of smog in the areas around them. In addition, oil-based boiler systems can hold back the purchase of household property since many buyers do not want the insurance headaches or responsibilities of maintaining or replacing oil boiler systems.
Converting your boiler system to natural gas reduces these negative consequences that come with oil-based systems. While newer, greener methods of heating your home will undoubtedly arise as green engineering methods become more advanced, natural gas is a great option if you're looking to be more environmentally friendly.
To help you better understand this green engineering process, we've outlined the pro's and con's of natural gas, what the conversion process will look like, and when an experienced contractor will be required to implement this process.
Discover the top ten inventive green engineering trends expected to
take over green building over the next year.
Natural Gas for Domestic or Commercial Use
Since natural gas is a natural bio fuel found within the earth, it has to be “mined” and processed before household or industrial boilers can use it as a form of energy. Natural gas can be found on shore and offshore.
Recently, to make the process greener, gas is extracted by natural pressure up out of the drill hole. Natural gas then is taken through a process to remove impurities and other unhealthy substances such as water, mercury, or hydrogen sulphide. This process does vary but maintains the same goal – appropriate gas for use.
The goal of extracting gas is to extract all of it and channel it through pipelines to houses and industrial buildings for use as energy.
Natural Gas and Boiler Function
Regardless of whether a boiler uses coal, oil, propane, or natural gas, the function of the boiler remains the same. A gas boiler sits above the burner which receives gas as fuel. The burner is lit by a pilot light and remains lit throughout the time the boiler is active. Regulating boiler function and production are the temperature gauge and thermocouple junction. The water within the boiler heats to the desired temperature before being distributed throughout the heating system via pipes and released through the radiators either as hot steam or heat.
Choosing Natural Gas as Fuel to the BoilerSystem
With the affordability gap between natural gas and oil continuing to broaden, it is no surprise that the conversion of boiler systems from oil to natural gas is on the increase. Not only is gas less sensitive to political and economic activity, consumers are inspired by the improved greenhouse effect natural gas has on the atmosphere. Consistent with other green engineering projects, natural gas emits significantly reduced emissions of sulphur oxide, particulate, and mercury.
At the end of the day, the main deciding factor is cost. The cost of oil-fueled boiler systems and oil continues to be high with not much concrete indication of these prices dropping in the near future. The price of oil continues to grow while natural gas cost seems to be within the range of $1.14 to $1.24 per gallon. Other incurring costs for oil-based boiler systems include the following:
- Air emission permits
- Removal of underground fuel storage tanks which often need insurance and leak monitoring
- Regular boiler cleaning to remove soot buildup
- Pumping costs
- Oil conditioning additives
- Preheating and storage heating
- Regular oil supply purchases
Besides these small costs that add up to a hefty budget, other oil factors play a role in motivating this green engineering conversion from oil to natural gas. This includes the environmental risks of oil leaks and spills, as well as the high levels of carbon dioxide emitted into the atmosphere further polluting the air.
The Benefits of Natural Gas Powering Central Heating System for Green Engineering
Natural gas is quickly becoming a popular form of fuel, especially within the United States. For this reason, natural gas boiler conversions are becoming a popular green engineering practice. Considering the benefits of natural gas, it’s no wonder that many homes are converting their boiler systems. Here are some of the benefits to natural gas:
- Natural gas is considered a clean fuel since its emissions contain a significant reduction in CO2.
- Natural gas is vital to the production of alternative and renewable energy.
- Natural gas is cost-efficient.
- The increase of total energy available to consumers is that of about 60 percent. Consumers receive a 92 percent usable energy from natural gas, whereas oil supplies consumers with a small 32 percent of usable energy.
- Natural gas is naturally odorless; what gives it an odor is the mercaptan which is added as a means to detect gas leaks.
- When leaks occur, natural gas disappears into the atmosphere, unlike oil leaks which result in bio hazardous oil spills in the environment.
Average Cost for Changing from Oil Boiler System to Natural Gas
Before converting a boiler system from oil to natural gas, factoring in costs is an important step in the process. These costs are considered to be an average, however, they should give a clear indication of how to budget and what the conversion entails from a monetary perspective.
The below table will give an average indicator of costs over a broad range of requirements for a new or converted boiler system:
Requirement | Cost |
New boiler -- this price will vary depending on the type of boiler required | $5,113 |
Testing the tank for leaks | $500 |
New tank | $1,500 |
Removing underground tank and replacing | $3,000 |
Soil testing | $400 |
Environmental cleaning | $3,500 |
Major ground cleanup | Up to $100,000 |
Installing a gas line | $1,500 |
Hooking up the house to the gas line with meters | $1,000 |
New chimney liner | $1,500 |
Removing old oil tank | $1,000 |
Permits | $200 |
Fire inspection | $75 |
From the above finance table, the cost of converting or replacing your oil boiler with a natural gas boiler will vary according to each situation and presented needs. For now, this is a good indicator of the costs that can be incurred. Please note that the above prices may reflect differently on your quote and merely serve as a guide.
The above requirements will also vary as per the situation, however, testing the tank and soil, connecting the house to the gas line and meters, new chimney liner, permits, and fire inspection are among the more standard tasks to be conducted before concluding the conversion of the boiler to natural gas.
Should the tank be underground, it is advisable to ascertain the scope of repairs or replacement required. With this being the highest cost in converting oil boilers to natural gas, a savings plan could go a long way in preparing for the conversion.
Combustion Parameters to Be Considered
When converting a boiler system from oil to natural gas, some combustion parameters should be taken into account. Within these parameters are indicators of the nature of natural gas which is a highly flexible, yet consistent, type of fuel. These considerations further assist in preparing for the conversion as well as giving a better understanding of what to expect from the conversion.
Boiler Thermal Performance Requirements
Maintaining the correct amount of burners within the boiler system is crucial in ensuring optimal heat and functionality. Too little or too many burners can result in eventual damage to the boiler system and burners. This will ultimately result in inefficient heating and increased expenses.
The range of heat inputs for industrial or home systems range from a minimum of 25 to 250 Mbtu/hr. This serves as a base line for heat and required burners. For more information, read here.
Emissions
Reduced emissions can be expected with natural gas, which is why this is considered a green engineering project. Mercury emissions are almost non-existent, allowing for natural gas to be less toxic to the overall atmosphere. Natural gas has minimal to no traces of sulphur, although traces of mercaptan and SO2 can be found. Natural gas does generate traces of Particulate Matter (PM) found in the combustion air flow. In addition, natural gas has lowered fuel-bound nitrogen with less air required for combustion.
Safe Gas Fuel Supply
Having access to gas supply is a basic requirement since natural gas will be used to produce heat in the central heating system after conversion. Thus, access to an existing gas line is required. Once this access has been established, further piping and valving is required to ensure that gas is transmitted safely and properly to the boiler. Adequate pressure for the system should be at a minimum of 25 PSI.
Updating the Burner Management System
The boiler system’s Burner Management System (BMS) should undergo an evaluation to maintain safe and proper use of the boiler system after conversion. The gas will be regulated by the Distributive Control System (DCS) which is the utility version of the BMS.
To further assist with regulating the safe use of gas within the boiler system, scanners should undergo an evaluation as a means to determine if they are sufficient or need replacing. The purpose of the scanner is to monitor the amount of high intensity radiation released into the UV zone. This is one of the disadvantages of natural gas since its radiation is much higher than that of oil or coal.
How to Convert Your Oil Boiler to Natural Gas: Green Engineering Best Practices
Although a green engineering professional is commonly contracted to convert a boiler system from oil to natural gas, a homeowner may have a role to play in this conversion. This does not remove the professionals completely from the process. On the contrary, installing the necessary equipment for a natural gas burner is best left to the professionals. Whether a homeowner works with a professional or a professional is consulted for the entire conversion, the following process remains the same:
Determine the Gas Line
An existing gas line should be determined. If a household utilizes gas for other appliances, the house is probably connected to a gas line. This should still be confirmed. If a house is not connected to a gas line, the local gas company should be contacted to arrange the installation of a gas line. This process can be enhanced if several houses in the same area are requesting a gas line.
Inspect Existing Equipment
Analyzing and inspecting existing equipment should best be left to professionals. The entire system needs to be evaluated in order to establish if the equipment is safe and well-equipped to efficiently convert to natural gas. Depending on this inspection, some equipment may need to be repaired or replaced and should be factored into the overall costs of converting a boiler system from oil to natural gas.
Expect Changes
Converting a boiler system to natural gas will entail several changes. The magnitude of these changes will be confirmed by a professional as they evaluate the existing boiler system. Some of these changes may include replacing copper pipes, converting the water heater to accommodate natural gas, and purchasing a chimney flue liner, should any size discrepancies arise.
Dealing with Old and New Equipment
All old equipment should be appropriately disposed of. Generally, gas companies are willing to assist with this disposal as part of their customer care.
Any new equipment installed in the boiler heating system should be HVAC approved. This will ensure that the conversion to natural gas remains efficient and effective. A professional should install the natural gas burner since the entire system can be assessed simultaneously.
Like many green engineering practices, the goal of the conversion from oil to natural gas is to maintain cost-efficiency and energy saving. This will impact costs, however, in the long-run, it should prove worthwhile in the end.
Consult a Green Engineering Professional
Although a homeowner can be involved in the conversion of their oil boiler to natural gas, much of the conversion should be done with the assistance of a professional that specializes in green engineering. The home owner’s role would be to ascertain budget feasibility, location of the tank, – above or underground - the requirements for a new boiler or a repaired boiler, and any known repairs.
The remainder of the scope of the conversion should be completed by professionals who understand the details of the conversion, the legal requirements to be followed, and green engineering best practices. They will be able to advise on ways to maximize heating efficiency within the boiler and central heating system. This will go a long way to reducing costs or removing unnecessary costs by recommending repairs or upgrades instead of replacing the entire boiler system.
Added Benefits of Natural Gas
By converting an oil boiler to natural gas, a home is connected to gas pipelines. With access to these pipelines comes the possibility of incorporating natural gas to power other appliances and other systems within the home. This may further reduce expenses while improving energy efficiency.
Key Takeaways
An oil to natural gas boiler conversion is a great project if you make your home more environmentally friendly. Green engineering is rapidly becoming a priority for many households, and their are many green engineering firms that would be happy to help you make your conversion a success. If you're considering undergoing this conversion, remember the following:
- Choosing natural has emits significantly less toxins into the environment when compared to oil
- Make sure combustion parameters are considered before beginning the conversion process
- Confirm where the gas line is located, and inspect any existing equipment for best results
- Consult a green engineering professional to evaluate the project to ensure smooth conversion
What other tips do you feel would aid to this process? Comment below and let us know. If you want to learn more green engineering tips and best practices, download our ebook "The Top 10 Inventive Green Engineering Trends for 2017" so you can see what's to come for green engineering.
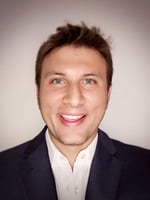
Michael Tobias
Michael Tobias, the Founding Principal of NY Engineers, currently leads a team of 150+ MEP/FP engineers and has led over 4,000 projects in the US
Join 15,000+ Fellow Architects and Contractors
Get expert engineering tips straight to your inbox. Subscribe to the NY Engineers Blog below.