Pouring Concrete with Cold Weather
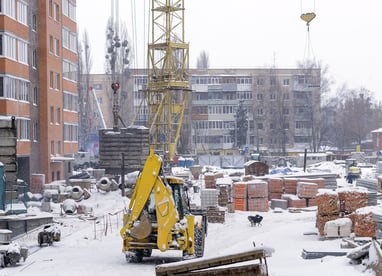
The process of pouring and curing concrete becomes more challenging in cold climates. Fresh concrete must be protected from freezing during the first 24 hours for it to set properly, since it will lose most of its strength if allowed to freeze. However, with proper safety measures and precautions, concrete can be poured successfully even in cold weather conditions.
Cold Weather Concreting
Cold weather concreting is defined by the American Concrete Institute (ACI) as “a period when for more than three successive days the average daily air temperature drops below 40 degrees Fahrenheit and stays below 50 degrees Fahrenheit for more than one-half of any 24-hour period.” Concrete sets best at 50-60°F, but in winter times the ambient temperature will likely fall under this range. The exothermic reactions that transform wet cement into concrete are slowed down as a result.
Construction administration services help you manage the weather and other risk factors.
If concrete freezes before it has cured to a strength that tolerates the expansion of ice, the final strength may be reduced by up to 50%. The water in the concrete mix will freeze and expand, causing it to become weak and brittle. Fortunately, there are several steps that can be taken to effectively pour and cure concrete during winter times. This article describes best practices and tips for cold weather concreting.
Preparation Tips
To achieve proper temperatures for curing concrete in cold weather, several measures can be implemented during the preparation stage.
Preheating water and aggregates: Heating some components of the concrete mixture will help achieve a proper temperature during pouring. Ready-mix companies can produce concrete that leaves the plant at approximately 65°F. On site, small amounts of concrete can be mixed with hot water, and it also helps to store aggregates in warm indoor locations.
Adjusting concrete components: The concrete mixture can use an increased cement ratio, or an accelerating chemical admixture can be added to enhance the curing process.
Using Portland cement Type III: This cement helps in setting without compromising the quality of concrete. It is ground finer and reacts faster than Type I, gaining strength faster.
Pouring Tips
While pouring concrete with cold weather, additional steps can be taken to ensure proper curing and setting.
Check the pouring surface: Pouring concrete on frozen ground will quickly change its temperature. The surface can be prepared with a heater to prevent quick cooling, allowing for the proper reactions to take place.
Use windbreaks: Windbreaks protects the construction site from winds that cause sudden temperature drops. The wind can cause a quick water evaporation in fresh concrete that is not protected, causing damage. Weather monitoring systems at construction sites are useful for project managers, especially during the winter.
Consider installing heated enclosures: Enclosures can be made of wood, polyethylene sheets, canvas or plastic. Electric or fuel-burning heaters can be used to within the enclosure. The safest combustion heaters are those with indirect-fired systems, where the burner is outside the enclosure. There are also hydronic systems, which circulate a mixture of glycol and water through the enclosure, using pipes or hoses.
The goal is ensuring the concrete temperature is at least 40°F while pouring, and keeping that temperature for as long as necessary. The specific requirements change depending on the application, but the concrete should not freeze within the first 24 hours under any circumstances.
Curing Tips
Once the concrete is poured, there are several tips that can be applied during the curing process. The goal is achieving maximum strength within the recommended period of time, according to the type of cement used.
Keep forms attached: If concrete is poured in forms, leave them in place for as long as possible. They help retain heat, especially at the corners and edges.
Use steam: Humidity levels tend to drop during cold weather. Steam can be pumped into the enclosure around the concrete, to maintain adequate humidity and temperature levels for curing.
Use thermal imaging: When the concrete is being cured, make sure its temperature is at least 40°F.
Check for concrete bleeding: While bleeding is common in concrete and it should not be an issue, make sure the water evaporates before finishing the surface. As mentioned before, curing takes longer with cold weather, so bleeding will usually start later than expected.
Control the concrete cooling rate: Gradually lowering the temperature within the concrete enclosure will protect it from cracking. When allowed to cool by itself, the concrete slabs can crack due to uneven cooling.
Use sealants: Concrete should always be sealed once it has cured. This will prevent water infiltration, while extending service life and lowering the risk of failure while curing. In reinforced concrete, sealants also protect the enclosed steel.
Conclusion
Concrete is one of the most widely used construction materials. However, additional precautions are necessary when concrete is poured and cured with cold weather. Risk management is an important element of construction administration, and this includes preparing for harsh weather conditions.
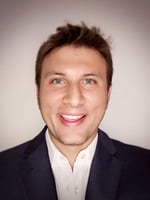
Michael Tobias
Michael Tobias, the Founding Principal of NY Engineers, currently leads a team of 150+ MEP/FP engineers and has led over 4,000 projects in the US
Join 15,000+ Fellow Architects and Contractors
Get expert engineering tips straight to your inbox. Subscribe to the NY Engineers Blog below.