Solving Low Water Pressure Issues in High-Rise Buildings
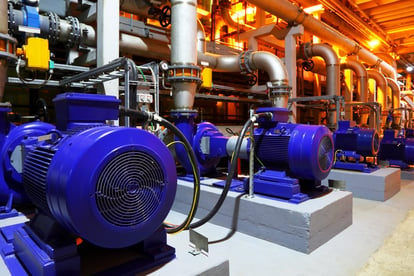
If water is delivered to plumbing fixtures with poor pressure, or not delivered at all, there are many possible causes. Sometimes the municipal water supply pressure is not enough to meet the needs of the building in question, requiring a pressure-boosting system. However, there also cases where internal plumbing issues hinder water distribution, even if the supply pressure is adequate.
When a high-rise building is showing water pressure issues, the first step is to identify the causes, since installing the wrong solution is a waste of money. For example, installing a booster pump when low pressure is due to clogged piping causes unnecessary energy expenses and may even cause pipes to burst.
Get a professional plumbing system design for your next building project.
Scenario #1: Adequate Water Supply Pressure and Plumbing System Issues
If the municipal water supply has an adequate pressure, but there are still plumbing fixtures with insufficient flow and pressure in the building, there are several possibilities. Clogged pipes are often found in older installations, where accumulation of rust and sediment over time causes a drastic reduction in the internal diameter of piping, occasionally blocking pipes completely. Sometimes the damage is evident on the surface as well, but a pipe can also appear to be in working condition while being clogged internally. The piping can sometimes be cleaned and restored, but may need a replacement if the damage is extensive.
Poor water pressure can also occur in newer installations if piping is specified too small due to errors during plumbing design. Clogged piping and undersized piping have the same effect - flow restriction and pressure drop.
Malfunctioning valves can also cause water pressure issues, as well as valves that have been left partially closed by accident. The best way to identify and locate plumbing system issues is getting a professional inspection of the building.
Scenario #2: Low Water Supply Pressure
If the municipal water supply lacks enough pressure at the service entrance, delivering water effectively to the upper floors may be impossible even with a brand new plumbing installation. There are also cases when the building is simply too high for the municipal water supply to reach upper floors without boosting equipment. The three main types of pressure-boosting systems approved by the NYC Building Code are the following:
- Elevated water tank
- Hydro-pneumatic pressure booster
- Water pressure booster pump
Elevated water tanks simply take advantage of gravity to deliver water at plumbing fixtures with an adequate pressure and flow rate. A pumping system replenishes the tank once water level falls below a determined level, and is turned off when the tank is full to avoid spillover. The pump ensures water availability, while the elevated tank provides the required pressure. The advantage of this configuration is that pumping horsepower is lowered, compared to a system where both pressure and flowrate must be established with a water pump.
The NYC Plumbing Code establishes a series of requirements to prevent the ingress of contaminants or vermin into these tanks. Most of these tanks are made of wood or steel in NYC, but other materials of equivalent mechanical properties are allowed. For a given storage capacity, a wood tank is less expensive but more demanding in terms of maintenance.
Hydro-pneumatic pressure boosters use an airtight tank that is filled with water, pressurizing the air inside until a specified value is reached, and at this point the pump is turned off. Since the water is being pushed down by the pressurized air in the tank, it can be delivered to plumbing fixtures at an adequate pressure even when the pump is turned off. As the water level in the hydro-pneumatic tank decreases pressure is reduced, and the pump activates again once the lower threshold value is reached. For this type of pressure-boosting system, the NYC Plumbing Code requires the installation of a pressure relief valve, selected and configured according to the tank’s maximum rated pressure.
Elevated water tanks and hydro-pneumatic pressure boosters both rely on a pump that is turned on and off as needed, but they differ in how the pump is controlled.
- The pump supplying water to an elevated water tank activates at the lower level and deactivates at the upper level. It does not operate immediately when water level starts to drop, in order to prevent short cycling.
- On the other hand, pumps delivering water to hydro-pneumatic pressure booster systems are turned off when the system pressure drops below a specified value, and back on when an upper pressure is established. Like in elevated tank systems, the pump is not turned back on immediately when pressure starts to drop, in order to avoid short cycling.
A water pressure booster pump operates directly on the water supply line to increase pressure. A very important design consideration is that pressure is reduced at the pump suction, so a cutoff switch must be installed to prevent cavitation, which can cause severe damage to the pump impeller and other system components. The NYC plumbing code requires the cutoff switch to activate whenever the pump intake pressure drops below 10 psi.
Keep in mind that plumbing system deficiencies and poor water supply pressure can be present simultaneously in a building, and the best way to determine this is through a professional assessment.
Importance of Engineering Design in Pressure Boosting Systems
Design services not only ensure that pressure-boosting systems meet NYC codes. They also prevent excessive pressure and flow, which have two negative consequences:
- They represent a waste of pumping power.
- Excessive flow increases the energy consumption of domestic hot water systems, since there is more water moving through them.
Rules of thumb can be a tempting approach when sizing mechanical and plumbing equipment, due to their simplicity. However, they typically result in oversized installations that are inefficient and bring additional maintenance issues.
The NYC Plumbing Code provides a table with the minimum flow and pressure that must be delivered for each type of plumbing fixture. When pressure fails to reach those values and the plumbing system is in good condition, a pressure-boosting system is necessary. In New York City, the municipal water supply pressure is generally enough for buildings up to five stories high. Above that point, a boosting system is typically required.
Meet building codes and save on water bills with a professional plumbing design. Nearby EngineersNew York Engineers has an 80% first-time design approval rate - write at info@ny-engineers.com or dial (786) 788-0295212-575-5300.
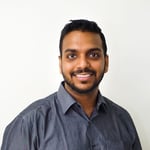
Anuj Srivastava
Anuj Srivastava is a principal partner at NY Engineers. He is known for his MEP franchise market knowledge. Anuj is currently leading a team of 100+ MEP/FP engineers and has successfully led over 1500 franchise projects in the US.
Join 15,000+ Fellow Architects and Contractors
Get expert engineering tips straight to your inbox. Subscribe to the NY Engineers Blog below.