The Role of Safety Managers in Maintenance Management
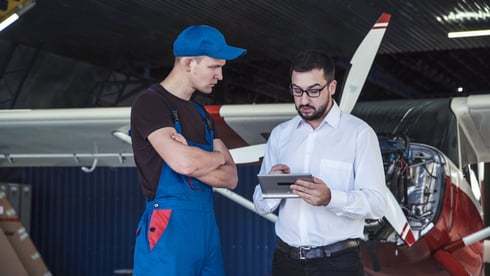
Safety management involves an array of activities aimed at reducing workplace hazards that could otherwise cause personal injury, facility damage or result in legal repercussions against an organization. In order to cultivate a robust safety culture, organizations engage safety managers who develop, spearhead the implementation and upgrade safety procedures in a facility in strict adherence to legal provisions.
Safety management roles vary based on the facility’s organizational structure and complexity. It is the duty of a safety manager to ascertain that a facility operates in accordance with the statutory health and safety standards, while at the same time developing proactive contingency plans to address probable emergencies.
A well organized maintenance department complements the efforts of a safety manager by ensuring that facilities and production equipment operate correctly and safely. Coherent maintenance programs eliminate incidences of unplanned breakdowns which may escalate workplace accidents.
Maintenance operations are high-risk activities that involve non-routine operations and must be undertaken within strict timelines. Maintenance personnel come to close contact with machinery to undertake corrective measures. In some cases, they are obliged to operate in confined spaces or at heights, increasing their exposure to hazards. Maintenance operations demand strict adherence to safety protocols as the probability of accidents due to human errors spiral while maintaining facilities.
Roles
1. Formulation of Safety Policies and Procedures
Safety managers are responsible for guiding maintenance teams and the entire organization towards accident free workplaces through the formulation of wholesome, realistic and understandable safety policies.
In order to accomplish this, the safety manager examines the provisions of the Occupational Safety and Health Act (OSHA). This lays the ground for the safety manager to perform a thorough health and safety audit of a target facility, evaluating dominant hazards and the inherent safety impacts of all equipment and systems. The safety audit scrutinizes the maintenance team’s work practices and their overall preparedness to respond to emergencies.
Facility occupants provide valuable information regarding daily operations and routine maintenance activities, offering invaluable insights into frequent safety issues. This helps the managers to identify additional safety aspects that may be overlooked during the safety audit. They highlight previous scenarios and expound on corrective measures that were adopted to keep the situation under control.
Collectively, the data from the safety audits, examination of maintenance and production plans, and the input of occupants constitute the backbone for the organization to devise and document a detailed and clear safety policy.
2. Monitoring Execution of Safety Policies
Safety managers oversee the implementation of all the documented safety policies, keenly evaluating the integration of the policies to facility maintenance operations. Physical anomalies identified during the audit must be immediately rectified, after which a proactive plan is adopted to prevent similar occurrences in the future.
During policy implementation, the safety manager liaises with senior management to provide adequate protective equipment and appropriate work tools for all maintenance teams. Protective equipment such as gloves, coveralls, safety boots, dust masks and goggles reduces exposure to hazards. Using the correct work tools lessens the overall maintenance workload.
The safety manager will frequently traverse the facility to supervise and enforce compliance to safety policies, detecting, recording and instantly correcting any policy violations. To gauge the success of the safety program, the managers assess the correct usage of PPEs and work tools, and examine the trends relating to the frequency of safety incidents within a facility.
3. Staff Training and Continuous Safety Assessments
The safety manager ensures that all maintenance personnel are privy to the facility's safety policies, promptly informing them of any changes. The manager conducts rigorous training through on-the-job training and provides visual or text materials for reference. The training period provides an opportunity for maintenance teams to seek clarifications on unclear clauses included in the policy.
For policies that are accompanied by the introduction of additional safety equipment such as alarms, the safety manager will guide sectional heads and maintenance teams in elaborating how the additional enhancements will affect their routines.
As technology advances, facilities are obliged to adopt multiple production and maintenance solutions in order to boost productivity and enhance safety. These changes affect safety policies requiring them to be continuously upgraded so as to compete favorably in a dynamic market. Safety managers are always assessing existing policies to identify loopholes and establish a database of emerging safety gaps in maintenance activities and proactively providing solutions to them.
4. Formulate Procedures for Reporting and Documenting Accidents
Despite the efforts by organizations to inculcate unique safety cultures in their facilities, isolated incidents summing up to 2.8 workplace injuries per 100 full-time workers were reported in 2020 to the US Bureau of Labor and Statistics (BLS). With such cases, it is vital that safety managers develop transparent systems through which maintenance teams can report and document accidents.
Workplace accidents, both minor and major, occur without notice leaving maintenance teams in a state of confusion. If not well managed, emergency situations balloon rapidly causing irreversible damage. While creating an accident reporting system, the safety manager outlines reliable emergency measures to keep accidents under control.
Part of the measures include safe evacuation plans in case of fires, basic first aid procedures, safe shutdown procedures and protective sheltering. The system must also provide mechanisms to account for all staff once the risk has been eliminated.
5. Formulation of Safety Awareness Campaigns
The best way for safety managers to test the readiness of maintenance teams to respond to emergencies in a facility is through simulated safety drills. Safety managers may at their own discretion formulate an awareness plan to verify the team’s acquaintance to existing safety procedures.
To encourage participation of team members in fostering workplace safety, the managers devise reward programs in order to compensate individuals who strictly follow the established safety guidelines. Safety awareness campaigns enhance staff familiarization to facility safety regulations while nurturing a positive safety culture among individuals.
Summing Up
The safety of facilities is a function of appropriate maintenance programs and the successful implementation of safety policies. Security managers are an integral part of any company’s quest to fully comply with the Occupational Safety and Health Act requirements. They are multi-skilled individuals who possess apt leadership and technical skills, whose roles within a facility complement and improve maintenance operations.
Rolling out a safety policy consumes a considerable amount of time and resources, requires a robust strategic plan and should be subjected to iterated tests to increase its chances of success. Safety managers must always monitor the implementation of safety policies, periodically updating the procedures to cater for new facility developments.
About-
Bryan Christiansen is the founder and CEO of Limble CMMS. Limble is a modern, easy to use mobile CMMS software that takes the stress and chaos out of maintenance by helping managers organize, automate, and streamline their maintenance operations.
Guest Post
New York Engineers always welcome guest posts that are relevant and informative.
Join 15,000+ Fellow Architects and Contractors
Get expert engineering tips straight to your inbox. Subscribe to the NY Engineers Blog below.