Understanding and Improving Compressed Air System Efficiency
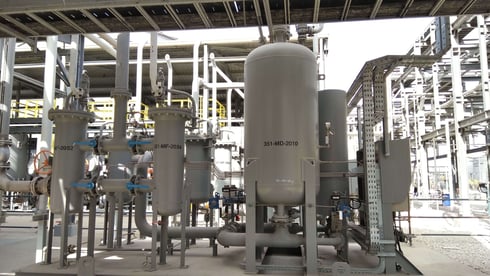
Compressed air systems are an integral part of manufacturing processes anywhere in the US, including Chicago. Despite this they are one of the most inefficient, expensive, and misused utilities available. Air is often considered free when used, but by the time it is finally used, it is anything but that.
Before we explain why this is so, more about compressed air system types available in Chicago, and the ways of driving energy and cost efficiencies in their use, it’s important to understand the prevailing regulatory context to them.
Regulatory Context of Compressed Air Systems
The current edition of all applicable regulatory codes should always be consulted prior to compressed air system specification, installation, repair, maintenance and operation. What follows here is for guidance purposes only.
The US Department of Energy (DOE) regulates the minimum efficiency of compressors based on the Energy Policy and Conservation Act. The DOE sets energy efficiency standards for one of two main types of compressed air system - lubricated rotary screw systems. In setting its standards, the DOE worked with compressed air manufacturers and the the Compressed Air and Gas Institute (CAGI).
DOE Building Energy Codes Program
The DOE Building Energy Codes Program on the other hand applies to all new compressed air systems with an installed compressor capacity of at least 25 hp. It also applies to all existing compressed air systems altered on the supply side except systems that include one or more centrifugal compressors for alternations.
Compressed Air System Types
An air compressor increases the pressure of inlet air by reducing its volume. Two broad compressed air system types are available for specification in Chicago that achieve this: dynamic oil free centrifugal and lubricated rotary screw systems.
1. Dynamic, Oil-Free Centrifugal Compressed Air Systems
Application: These oil-free systems are used over a wide range of industrial and process applications requiring large volumes of high-quality air.
Compressor description: Dynamic, oil-free centrifugal air compressors increase air velocity, which is then converted to increased outlet pressure. These compressors are also classified as radial and axial flow types. These centrifugal impeller compressors develop pressure by dynamic action. Their typical horsepower range is 300-3000 hp and they are normally driven by an electric motor. They are inherently oil-free.
In these systems, a wet receiver stabilizes system pressure, serves as a demand reservoir and holds moisture, and an air dryer provides the correct pressure dew point and traps remaining moisture. If either fail, a coalescing filter provides protection. A dry receiver can also be installed to stabilize pressure during high demand and to act as a reservoir.
2. Lubricated Rotary Screw Compressed Air Systems
Application: These lubricated systems are used where compressed air with high purity is required.
Compressor description: Lubricated rotary screw compressed air systems use a lubricant to alleviate friction between moving parts of manufacturing equipment such as robots, pneumatic tools, and paint sprayers. In lubricated rotary screw compressors, the lubricant seals clearances and removes heat of compression. Lubricant viscosity depends on the operating ambient temperature range. It should offer adequate lubrication for bearings and rotors at operating temperature and have a low enough pour point to provide fluidity at a low starting temperature. These compressors tend to have the largest rated output. Their use is significant as they account for under 1% of annual compressor shipments but represent an estimated 80% of total annual electricity consumption by air compressors.
Rotary systems not only consist of a wet receiver, an air dryer, a coalescing filter and a dry receiver but also a charcoal filter between the coalescing filter and dry receiver to eliminate extraneous oil vapor.
The natural inefficiency of compressed air systems
Compressing air is naturally inefficient. Most of the electrical power consumed by a motor that drives an air compressor heats the air with the following consequence:
> Air that exits a compressor then needs to be cooled
> A fan and an air or water cooled heat exchanger is then needed, consuming more energy
> Once compressed, air is delivered at a certain pressure to end users
> As it is transported, further losses and inefficiencies arise
> Beyond this, compressed air is often used incorrectly or for unintended purposes.
The cost of compressed air systems
Compressed air is commonly accepted as a utility after water, electricity and natural gas but is expensive.
To calculate the cost of compressed air the following formula can be used:
cost ($/year) = motor bhp x .746 x hrs of operation/yr) x electric rate ($/kwh) / motor efficiency
From this it can be seen that: if the system motor has a lower bhp the system is used less time each year, the system has a lower electric rate or a higher motor efficiency, cost savings will result.
The need to optimize compressed air systems for both cost savings and greater energy efficiencies
A research study “HAP – Best Practice Catalog – Compressed Air Systems” reveals there are no best practices directly associated with the efficiency and capacity of compressed air systems but instead reliability/operations and maintenance oriented best practices.
Others elaborate that for compressed air system improvement it is not maintenance personnel but operators who should be considered first.
In this way, operators should be trained and encouraged to seek ways to reduce demand for compressed air, and the operational time a system is used for, to avoid air misuse, look for an alternative and to be aware of maintenance inspection requirements.
Afterwards, routine maintenance inspections of compressed air systems can take place to optimize systems by undertaking the following:
- A System Audit.
- A Leak Detection and Repair Program.
- A Supply and Demand Analysis.
- An End Use Survey.
System Audit
Taking a systems approach can help eliminate issues. It’s worth considering the entire compressed air system, not just a single compressor to help reduce energy use. Look at the system globally, from the compressor air inlet right to the end use of the air.
Air Leak Repair Program
Leaks are common a variety of locations including, pipe fittings, condensate drains and compressor blow-downs, hoses, fittings, hand tool connections and spray applicators, valve stems and the plastic bowls at the foot of filters, regulators and lubricators.
Establish a formal air leak repair program. Locate leaks, using ultrasonic air leak detectors as necessary, throughout a compressed air system, tag and prioritize them, and repair the largest first. Keep compressed air dry filtered to help eliminate dust and sludge and prevent new leaks forming.
Supply and Demand Analysis
Supply and demand sides of a compressed air system are important. Consider them together when making compressed air system decisions (compressor type and capacity, location, receiver tanks, piping size and arrangement, selection and so on). Evaluate existing compressor control systems too to determine whether they are still appropriate.
End Use Survey
Carry out an End Use Survey to identify each end use and rank each end use by size, in terms of the required volume and the required supply pressure. Use the survey results to assess if your system should have one or more standalone compressors or storage tanks for particular end uses and perform optimization measures such as:
- Operating air compressors at lowest possible discharge pressure.
- Eliminating nozzle use, or if impossible, using engineered nozzles for blow-offs.
- Eliminating improper use of compressed air, which causes artificial demand
Thirdly, perform other maintenance and part replacement of compressed air systems to optimize systems further, such as:
- Visual inspections of air compressors to assess loose connections, belt conditions, paint condition, hot spots, stuck condensate drains and identify high vibration, oil leaks or inadequate cooling.
- Taking oil samples, where present, and analyzing for water intrusion, particulate contamination and useful life.
- Conducting water analysis to determine any treatment needs, such as hardness treatment
- Conducting vibration and bearing temperature monitoring.
- Verifying compressor sequencing and operation by checking compressor load and unload times against initial design intent.
- Observing load and unload pressure setpoints while checking load and unload frequencies.
- Replacing belt guards
- Replacing timer drains with zero-loss drains
- Greasing all bearings.
- Periodically cleaning the air/oil separator, coolers and heat exchangers on the supply side
- Changing filters regularly
End Note
The information provided here confirms the significance of the need to optimize compressed air systems to achieve efficiency and cost savings through appropriate specification, maintenance, operation and use.
Do not hesitate in consulting engineering professionals familiar with air compressor systems to assist in the specification of a new compressed air system or the alteration or repair to an existing system in Chicago that is as efficient and cost effective as possible.
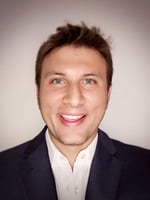
Michael Tobias
Michael Tobias, the Founding Principal of NY Engineers, currently leads a team of 150+ MEP/FP engineers and has led over 4,000 projects in the US
Join 15,000+ Fellow Architects and Contractors
Get expert engineering tips straight to your inbox. Subscribe to the NY Engineers Blog below.