Variable Speed Pumping Systems
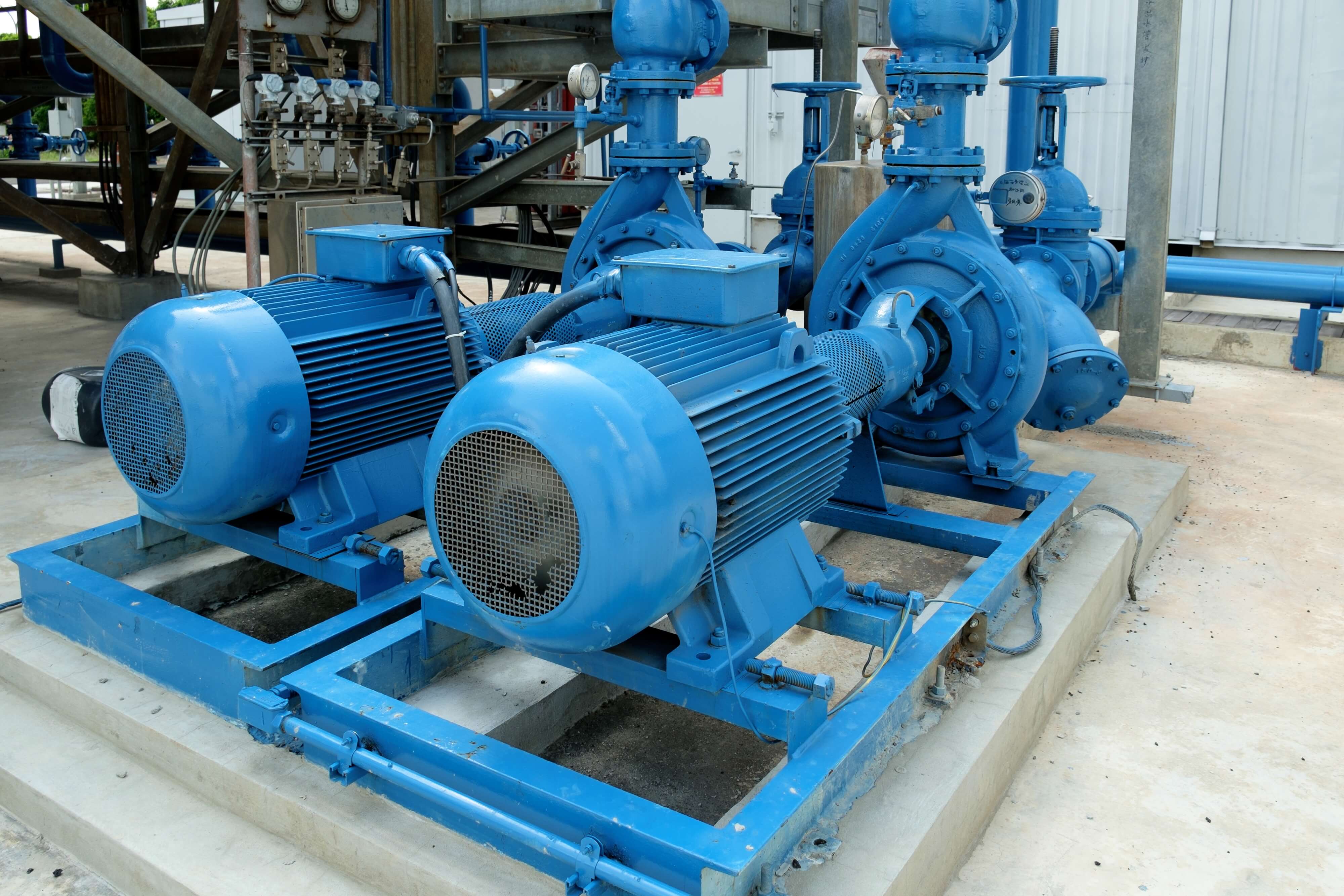
Variable speed pumping systems are often used to boost the pressure of the local water supply, especially in high-rise constructions. Pumps also have applications in HVAC, fire protection and industrial processes.
Building installations do not have a constant demand for water, and the flow provided by pumping systems must be modulated to match demand. There are three main ways to achieve this:
- Using a control valve at the pump outlet to restrict flow.
- Using a recirculation valve to send the unused water flow back to the pump inlet.
- Controlling pump speed to adjust flow and match system demand.
Variable speed pumping systems can adjust the rotating speed of the impeller to modulate water flow, which is much more efficient than using valves. Flow restriction and flow recirculation both represent a waste of pumping power, driving up electricity expenses. Only variable speed pumping systems can optimize their operating costs, consuming just the necessary power to establish the required water flow.
Pumps and their associated components can be expensive, especially in large installations. To avoid purchasing oversized equipment, pumping systems must be specified with the right capacity. Working with qualified MEP engineers is strongly recommended to achieve high performance and optimal costs.
Understanding the Main Types of Pumps
Although there are many pump designs available, most can be classified as either centrifugal pumps or positive displacement pumps. Regardless of their type, pumps are normally driven by an electric motor or a combustion engine. However, electric motors are the most cost-effective option for most building owners.
Centrifugal pumps have a rotating impeller with curved blades, which increase the pressure of water by accelerating it towards the edges. Centrifugal pumps can be further classified into three subtypes based on their flow direction:
- Axial flow pumps move water along the same direction of the impeller shaft.
- Radial flow pumps move water at a 90° angle with respect to the shaft.
- Mixed flow pumps are intermediate, producing flow at an angle less than 90°.
Positive displacement pumps move fluid in “pockets” at regular intervals. Based on their construction, positive displacement pumps can be described as reciprocating or rotary.
- Reciprocating pumps use a cavity that expands and contracts to move water, controlling the flow direction with check valves.
- Rotary pumps trap water in cavities around a rotor, and displace it towards the outlet.
Other than physical construction, an important difference between centrifugal and positive displacement pumps is how they respond to pressure. Centrifugal pumps have a direct relationship between flow rate and pressure, and flow decreases when they work against a higher system pressure. On the other hand, positive displacement pumps can sustain a constant flow under variable pressure, due to how the pumping process is carried out.
How Variable Speed Pumping Systems Save Energy
As discussed above, there are three options to control the water flow provided by a pump: flow restriction, flow recirculation and variable speed. However, speed control is the most efficient option because the other two waste pumping power.
- When a pumping system is controlled with flow restriction, the pump consumes power to compensate the pressure loss across the control valve.
- A similar principle applies when the flow is controlled with recirculation since the unused water flow represents wasted power.
Speed control can be achieved by adding a variable frequency drive (VFD) to the pump motor. A VFD modulates the voltage and frequency of the power supply, and the rotational speed of the pump changes accordingly. If the demand for water is below the rated flow of the pump, the VFD slows it down until the flow provided matches demand.
Before adding speed control to a pumping system, a very important step is verifying that the pumps and the proposed VFDs are compatible. There are various pump designs and VFD models, and not all of them are compatible. Some VFDs are exclusive for centrifugal pumps, others are exclusive for positive displacement pumps, and certain models offer compatibility with pumps of both types.
Variable Speed Pumping Systems with High-Efficiency Motors
Variable speed pumping systems offer the most efficient configuration, but optimal performance cannot be achieved if the pumps still use inefficient motors. NEMA Premium Efficiency motors have the highest efficiency rating in the industry, and you can achieve the lowest possible pumping costs by combining these motors with speed controls.
NEMA Premium Efficiency motors are available for a wide range of applications, and their rated power goes from 1 hp to 500 hp. These motors can save thousands of dollars each year when they replace older and less efficient units. They are very useful in pumping systems since their continuous operation provides an excellent chance to save electricity.
When deploying speed controls and efficient motors for pumping systems, it is also important to have reliable electrical protections. Variable frequency drives and NEMA Premium Efficiency motors can have a high upfront cost, and protecting that investment is very important. A reliable electrical installation also provides safer working conditions for maintenance personnel.
Key Design Considerations for Variable Speed Pumping Systems
Like many other mechanical installations, pumping systems can experience noise and vibration issues due to poor design decisions and inadequate maintenance. Periodic inspections are recommended to make sure all system components are working correctly. Some common causes of vibration are inadequate equipment supports, unbalance and misalignment. Controlling vibration is very important; it can speed up the mechanical wear of system components, increasing maintenance expenses.
When variable speed pumping systems are deployed as part of an HVAC installation, the design process must consider the entire installation and not only the hydronic piping. To take advantage of a variable speed pumping system, HVAC installations must also be capable of adjusting the air supplied by ventilation systems, and the cooling output of chillers and boilers.
Variable speed pumping systems provide an excellent opportunity to save energy in applications where large amounts of water are used. However, the benefits can only be achieved if the system is designed correctly and compliant with local codes. Professional design services from MEP engineers are strongly recommended.