5 Common Plumbing Issues in High-Rise Buildings
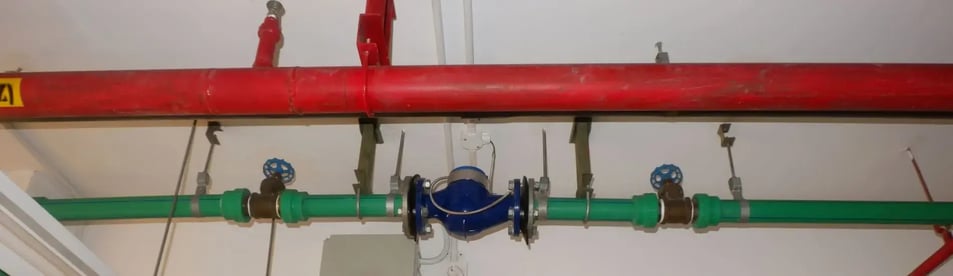
Managing a high-rise building goes beyond basic upkeep; it involves ensuring all systems, including plumbing, run smoothly. Optimizing plumbing systems during the design phase is ideal. Commercial plumbing is complex, and unexpected issues can cause disruptions and costly repairs.
High-rise buildings are tall structures, typically over 75 feet (23 meters) or about 7 to 10 stories, designed for residential, commercial, or mixed-use purposes. They require specialized structural, mechanical, and safety systems due to their height, including elevators, fire protection, and advanced HVAC systems for occupant comfort and safety.
High-rise living offers the best urban experiences, but it also comes with unique plumbing challenges. Residents of high-rise apartments and condos often encounter plumbing issues that require specialized solutions. Read on to learn about MEP design challenges for High-Rise Buildings. Here are the 5 most common plumbing issues you might deal with in high-rise buildings.
1. Insufficient or Excessive Water Pressure
Issue:
In tall buildings, water pressure can be insufficient on upper floors due to gravitational loss of pressure. Conversely, excessive pressure on lower floors can cause damage to fixtures and systems, leading to leaks and inefficiencies.
Solution:
Booster Pump Systems: Install pressure booster pumps to ensure adequate pressure at higher levels. Variable-speed pumps can adjust pressure according to demand, ensuring balanced water distribution throughout the building.
The global Booster Pump market size is estimated to be worth USD 2643.9 million in 2021 and is forecast to be a readjusted size of USD 3329.7 million by 2028 with a CAGR of 3.3% during the review period.
Pressure-Reducing Valves (PRVs): Install PRVs on lower floors to prevent damage from high pressure. These valves help maintain a balanced pressure distribution, ensuring the longevity of your plumbing systems.
2. Suds Zone
Issue:
In high-rise buildings, the "suds zone" refers to areas where wastewater from upper floors can cause suds to back up into lower-level fixtures, leading to blockages or contamination.
Solution:
Separate Header for Lower Floors: Implement an additional header specifically for the lower floor fixtures. This separate piping system will help isolate the lower-level fixtures from the wastewater generated on upper floors, significantly reducing the likelihood of suds backing up into these fixtures.
3. Water Hammering
Issue:
Water hammering occurs when a sudden change in water flow causes shock waves in the pipes, leading to loud noises, vibrations, and potential damage to the plumbing system.
Solution:
Water Hammer Arrestors: Install water hammer arrestors at strategic points, such as near appliances or fixtures prone to sudden shut-offs, to absorb the shock waves. These devices help protect your plumbing system from damage and reduce noise disturbances.
Water-hammer Arrestor Market size reached USD 9.2 Billion in 2022, to reach USD 12.5 Billion by 2032, exhibiting a growth rate (CAGR) of 3.2% during 2023-2032.
4. Water Heater Placement (Cellar vs. Roof)
Issue:
Deciding whether to place water heaters in the cellar or on the roof can significantly impact efficiency, maintenance, and safety.
Solution:
Cellar Placement -
Pros: Easier maintenance access, centralized location for distribution, potentially lower installation costs.
Cons: Longer pipe runs can lead to heat loss, increased energy usage, and longer wait times for hot water at upper levels.
Roof Placement -
Pros: Shorter pipe runs for upper floors, reducing heat loss and providing faster access to hot water.
Cons: Increased structural load on the roof, potential maintenance challenges due to weather exposure, and more complex installation.
Hybrid System: In some cases, a hybrid approach using multiple smaller heaters placed at intermediate levels (e.g., every few floors) can balance these issues effectively. This method combines the benefits of both cellar and roof placements while minimizing their respective drawbacks.
Another solution for the water heater placement is to be placed locally inside the apartment. This can help minimize the longer hot water pipe runs in the shafts/building and in case of a failure of the water heater, the entire building doesn’t get disrupted.
5. Noise Control
Issue:
High-rise buildings often face noise issues due to the vibration and operation of plumbing equipment. Uncontrolled noise can negatively impact the comfort of the occupants.
Solution:
Noise Reduction Measures: Implement noise reduction measures such as vibration isolation pads or acoustic enclosures to minimize the impact of equipment noise on building occupants. Using sound-absorbing materials and strategic placement of equipment can significantly reduce noise levels. Also, keeping piping installation to as minimum as possible can help reduce Noise.
Best Practices in High-Rise Plumbing Design
Vertical Stacks
Position vertical stacks (for waste, vent, and water supply) close to each other to minimize the length of piping and reduce construction costs. Ideally, they should be located in core areas to consolidate their paths, which streamlines maintenance efforts and improves efficiency.
Accessibility
Ensure easy access to plumbing components for maintenance and repairs. This includes planning for maintenance shafts and access panels. Accessibility is key to effective long-term management of plumbing systems in high-rise buildings.
Pipe Material
Use materials suited to high-rise conditions. PVC is commonly used for drainage, while PEX or copper might be used for supply lines. Each material has its own advantages and limitations, so choose wisely based on the specific needs of your building.
Energy-Efficient Hot Water Systems
Consider energy-efficient hot water systems, such as central water heating systems or on-demand water heaters, to reduce energy consumption and operational costs. Properly insulated hot water pipes can minimize heat loss and improve energy efficiency.
Fixtures and Fittings
Specify water-efficient fixtures and fittings, such as low-flow faucets, showerheads, and toilets, to promote water conservation. These choices reduce water usage without compromising performance, contributing to sustainability and cost savings.
Conclusion
Plumbing systems may appear static compared with mechanical systems, but they also involve significant engineering challenges. A poor design and installation process can lead to issues like inadequate venting, backflow and corrosion. However, many plumbing issues can be prevented simply by working with a qualified engineering company.
Correct plumbing design and maintenance are essential for a smoothly operating high-rise building. By proactively addressing common issues, you can prevent costly repairs and ensure a comfortable environment for building occupants. Trust NY Engineers for expert guidance in optimizing your plumbing system, ensuring efficiency, safety, and sustainability. For tailored advice and solutions, consider reaching out to a professional in the field.
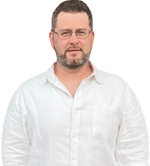
Keith Fink
Keith is the Franchise Brand Manager at NY Engineers, Keith is all things related to our project portfolio, brands and all things you need to know before we start your project.
Join 15,000+ Fellow Architects and Contractors
Get expert engineering tips straight to your inbox. Subscribe to the NY Engineers Blog below.