Top 4 Benefits of Prefabrication in Construction Industry
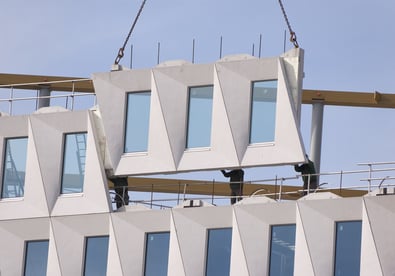
Construction and manufacturing both deliver a finished product by transforming raw materials. However, there are important differences: manufacturing focuses on large batches of identical products in controlled factory environments, while construction deals with unique projects that are built in exposed sites. As a result, manufacturing wastes a reduced percentage of the input materials, and quality control is simpler.
Prefabrication is a very promising concept for building developers, since it brings many benefits of manufacturing. Buildings are assembled from modular elements that are produced off-site, reducing the scope of work and man-hours at the project location. A controlled factory environment is also safer for the project staff, compared with an active construction site.
Optimize the construction process of your next building project.
Prefabrication Reduces Material Costs and Waste
With a conventional construction process, all materials are delivered to the project site to be transformed into a building. However, this approach turns construction into a wasteful process:
- Construction waste is often a mix of materials, which is very difficult to separate for use in other projects. As a result, a large volume of construction materials ends up in landfills instead of buildings.
- Quality control is more difficult in a project site, compared with a factory floor. Some construction materials are wasted due to incorrect use or damage - broken bricks and floor tiles are an example.
- Materials that come in predetermined shapes or sizes must often be cut before installation, and leftover pieces are frequently wasted. For example, electrical conduit is purchased in 10’ pipes, and a circuit that measures 28’ will leave you with 2’ of conduit. Unless another circuit requires just that amount, a piece of conduit is wasted.
- Nails, bolts and other small construction materials are easily dropped in project sites, especially when they are installed in hard-to-reach places.
- Exposure to the weather can damage some construction materials.
- Since project sites are more exposed than a factory floor, there is also a constant risk of material theft.
Contractors can implement waste management practices, but some forms of waste are unavoidable even when materials are used efficiently. However, since prefabrication is carried out in a controlled factory environment, recycling and waste reduction are simplified.
When materials are used more efficiently, project costs are reduced accordingly. Prefabrication achieves further cost efficiencies by allowing automation in a factory environment, reducing the man-hours required in a project.
Prefabrication Accelerates the Construction Process
When the entire building process is completed outdoors, construction may be suspended due to external factors like unfavorable weather. However, this issue is minimized with prefabrication, since production can continue in a factory floor under any weather conditions.
Regardless of how a building will be used, fast construction is always beneficial for the owner:
- Owners who are currently renting a building can get rid of rent payment.
- Even if clients are using another building owned by them, it is freed up for rent or sale once they move to the new building.
- If a project involves residential or commercial spaces for rent, a swift completion means that the owner can collect rent payments earlier.
Prefabrication Minimizes Disruption Around the Project Site
Construction involves heavy machinery in constant movement and frequent material deliveries, while producing plenty of noise. Also, material deliveries and truck movement can disrupt traffic when a project is located on a busy street.
By moving construction work off-site, prefabrication minimizes disruption for neighbors. Although the modular components must be delivered to the project site, handling finished products is easier that working with basic materials.
Prefabrication Achieves Synergy with Advanced Design Tools
3D modeling tools have a well-established role in manufacturing, but the concept is relatively new in the building sector. Since prefabrication brings part of the construction process to a factory environment, it allows automated manufacturing methods that are based on digital component models. Machine-tools controlled by CNC robots are a well known example.
Building Information Modeling (BIM) can produce highly detailed documents and specifications, but meeting these requirements in an exposed construction site is a significant challenge. On the other hand, a controlled factory environment allows improved quality and higher accuracy.
Concluding Remarks
There is a common misconception that a prefabricated building is more expensive than one built with traditional methods. It is true that prefabrication consumes large amounts of resources upfront, while material expenses are spread more evenly during the project with traditional construction. However, when prefabrication is planned and implemented correctly, it reduces total project costs.
Prefabrication also involves a learning curve for project staff members, who may be used to decades of traditional construction methods. However, the work of supervisors and contractors is actually simplified with prefabrication. Consider that the design approach must be changed slightly, since the building must be specified in terms of modular components produced off-site.
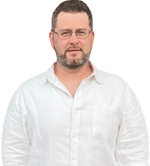
Keith Fink
Keith is the Franchise Brand Manager at NY Engineers, Keith is all things related to our project portfolio, brands and all things you need to know before we start your project.
Join 15,000+ Fellow Architects and Contractors
Get expert engineering tips straight to your inbox. Subscribe to the NY Engineers Blog below.