Ventilation Options for Residential Buildings
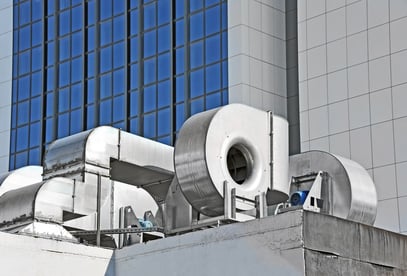
All habitable buildings require ventilation, and when this system has been implemented incorrectly or is malfunctioning, the poor air quality that ensues can have negative consequences such as unpleasant odors and health issues.
Ventilation can be classified into two subcategories, natural and mechanical ventilation. As implied by its name, natural ventilation is that which happens spontaneously thanks to air temperature gradients and convection; while mechanical ventilation is that which relies on equipment that consumes power, such as fans or air-handling units.
Get a ventilation design that meets code, while improving your indoor air quality.
For living areas, the New York City Mechanical Code requires the mechanical ventilation system to provide an airflow equivalent to the greater of the following:
- 0.35 air changes per hour, calculated based on the total floor area
- 15 cfm (cubic feet per minute) per person
Any space that is unheated or kept below 50°F and not subject to continuous occupation is exempt from these requirements. There are also special requirements for kitchens and bathrooms:
- Kitchens: 100 cfm (intermittent) or 25 cfm (continuous)
- Bathrooms: 50 cfm (intermittent) or 20 cfm (continuous)
Natural Ventilation Through Operable Windows
The main advantage of using operable windows for natural ventilation is that the energy cost is zero, since there are no injectors and extractors drawing power. The drawback of natural ventilation is that it is insufficient by itself in many applications, where the NYC Mechanical Code points it out and makes mechanical ventilation mandatory.
Regardless of whether mechanical ventilation is mandatory or optional, Chapter 12 of the NYC Building Code requires natural ventilation for all habitable spaces, and the allowed means of ventilation are windows and glazed doors. In the specific case of occupancies classified as Residential Group R-3, skylights and translucent panels are also valid as natural ventilation means. The following requirements are set forth:
- The total area of windows or similar ventilating means must be at least 5% of the total floor area of the habitable space
- Each individual window or opening must have a glazed area of at least 12 square feet, of which the openable area must be at least 6 square feet. In bathrooms and toilet rooms, the minimum glazed area per window is 3 square feet, with an openable area of 1.5 square feet
- Adjacent rooms connected through a door are considered separate spaces for ventilation purposes: requirements must be determined individually for each
- If there is a mechanical ventilation system supplying at least 40 cfm of fresh air, the required area of windows is reduced to 2.5% of total floor space. The required openable area per window is also reduced to 5.5 square feet
It is important to note that, whenever there is a mezzanine or a split-level room, the total floor area must be taken into account to design ventilation, not just the area of the lower level.
Properly sized and functioning windows are crucial for meeting these ventilation requirements. In cases where windows are irreparable, property owners typically consult a replacement windows company to meet all code requirements for glazed areas and operability.
Compartmentalized Mechanical Ventilation Through PTAC or ERV Units
When mechanical ventilation systems are required by codes, there are two main approaches: using centralized systems, or compartmentalizing them by dwelling unit. The second approach is viable with both packaged terminal air conditioners (PTAC) or energy recovery ventilation (ERV) units.
The main advantage of this approach is isolation between dwelling units, which increases overall air quality and allows individual and independent control of ventilation systems.
PTAC Units
Packaged terminal air conditioners operate on the same principle as window-type air conditioners: they are installed directly between the ventilated space and outdoors, drawing intake air and heating or cooling it according to current HVAC needs. The advantage of PTACs is that they consolidate heating, cooling and ventilation into a single unit, and are free from ductwork.
ERV Units
Energy recovery ventilation is a very energy-efficient alternative, which is based on using the exhaust air to precondition the intake air and reduce the total cooling or heating load. Their basic principle is the following:
- In the summer, the exhaust air is used to precool and dehumidify the intake air
- On the other hand, in the winter the exhaust air preheats and humidifies the intake air
It is important to note that ERV units may only be able to meet the full HVAC load under specific temperature and humidity conditions. Otherwise, they must operate in conjunction with an air conditioner or heater
Outside Air Injection to Corridor and Extraction Through Toilet Exhaust
The NYC Mechanical Code does not allow the exhaust air from bathrooms to be used for ventilation of other areas, but drawing in air from other building areas is valid. In the case of apartment buildings, a common injection system can provide air to corridors, which then enters individual dwellings before finally being exhausted by toilet fans. With this ventilation system, there are some important considerations:
- Bathroom extractors deal with the entire ventilation load of each apartment, and they must be sized accordingly. The NYC Mechanical Code allows a combined exhaust system for the kitchen and bathroom
- The injectors providing the outdoor air supply for each corridor must provide an airflow that balances with the combined exhaust of all individual apartments
When installing the air exhaust, there are several space clearances that must be taken into account:
- Two feet away from windows belonging to the same apartment
- Four feet away from windows of adjacent buildings or belonging to another occupancy type in the same building
- Ten feet away from any air intake opening, and ten feet above the public sidewalk
A final consideration is that corrosion-resistant grilles, screens or louvers are required for all intake and exhaust openings. The opening size must be between 1/4 and 1/2 inch
Simplicity is the main advantage of this ventilation system. When all doors in a corridor are closed, positive pressure tends to build up in the corridor while negative pressure builds up inside dwelling units. However, the Mechanical Code does not consider this an issue and pressure tends to balance out throughout the day as apartment doors are opened and closed
The main limitation of this approach is that compartmentalization is poor, which has some effects that may be detrimental for overall ventilation system performance. The impact of the stack effect in particular can be significant:
- When the outdoor temperature is lower than that of the building, air tends to leak into the building at the lower levels and out of it at higher levels
- The opposite effect occurs when the outdoor temperature is warmer: air tends to leak into the upper floors and out of the lower ones
The overall effect on ventilation equipment is increased energy consumption and reduced performance:
- In floors where outdoor air tends to leak in, extractors have to work harder
- On the other hand, levels where air leakage is directed outward tend to have air quality issues – air may be drawn in from other levels, carrying odors or pollutants
Individual Mechanical Ventilation Risers for Each Apartment
Building an individual riser for each apartment offers excellent control over ventilation, since the exhaust from each unit is completely isolated from that of the rest. Issues with the stack effect are also prevented – since each dwelling unit has a dedicated ventilation system, air tightness between different areas can be maximized without compromising the overall air quality. Therefore, this ventilation approach enhances the overall energy efficiency of a building because isolated systems don’t have to operate against bulk air movements.
The efficiency of this ventilation layout is further enhanced by the fact that each system can be controlled individually, something which is not possible when a single injection system provides the air intake for an entire floor. Humidity control is also improved when ventilation is compartmentalized by dwelling unit.
Of course, installing a dedicated ventilation riser for each apartment involves a higher upfront cost, since each unit has individual injection and extraction systems, and it may only be a viable option in new constructions due to space requirements.
General Energy Efficiency Recommendations
Ventilation system performance can be greatly enhanced with the use of variable frequency drives. Basically, a VFD adjusts fan speed according to the ventilation load, instead of cycling it on and off. Speed control is superior to duty cycle reduction because its savings are quadratic, while duty cycle reduction only provides linear savings.
- A fan running with a duty cycle of 75% consumes around 75% of the energy compared with another of the same characteristics operating all the time.
- On the other hand, a fan running at 75% speed only draws around 42% of the power consumed by a fan running at full speed
- In this scenario, duty cycle reduction to 75% yields 25% savings, but running the fan at 75% speed saves 58% of the energy. In other words, speed control yields 33% extra savings.
Along with space heating and cooling, ventilation plays a key role in maintaining optimal indoor conditions for human health and comfort. There are various potential system layouts, each with advantages and limitations, and at the end of the day the optimal choice is determined by project conditions and available budget. Compartmentalized ventilation systems tend to have a superior energy efficiency at a higher cost; while centralized systems tend to suffer from the stack effect in taller buildings, but are cost effective in lower height buildings where usage habits are similar across separate dwelling units.
Editors Note: This post was originally published in November 2016 and has been revamped and updated for accuracy and comprehensiveness.
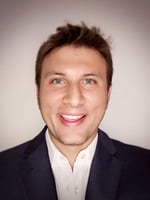
Michael Tobias
Michael Tobias, the Founding Principal of NY Engineers, currently leads a team of 150+ MEP/FP engineers and has led over 4,000 projects in the US
Join 15,000+ Fellow Architects and Contractors
Get expert engineering tips straight to your inbox. Subscribe to the NY Engineers Blog below.