What Is a Backflow Preventer and How Does It Work?
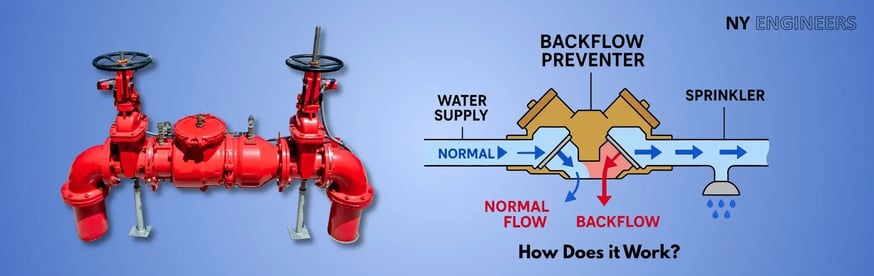
Backflow preventers serve as critical safety devices that protect our drinking water supply from contamination.
These specialized assemblies prevent contaminated water from flowing backward into clean water systems, safeguarding public health and ensuring compliance with municipal water regulations.
Understanding backflow prevention systems becomes essential for building owners, facility managers, and engineers responsible for maintaining water quality standards.
This comprehensive guide examines the fundamental principles, types, and applications of backflow prevention technology in modern building systems.
Understanding Backflow and Its Risks
Backflow occurs when water flows in the reverse direction from its intended path, potentially allowing contaminated water to enter potable water supplies.
This phenomenon poses significant health risks and can result in costly remediation efforts.
As per the Environmental Protection Agency (EPA) Report, backflow incidents require an average of 500 hours to remediate at a cost of approximately $14,800 per event.
Primary Causes of Backflow
Back Siphonage: This occurs when negative pressure develops in the supply piping, creating a vacuum effect similar to drinking through a straw. Common causes include:
- Water main breaks
- Fire hydrant usage
- High water demand periods
- Pump failures in the distribution system
Backpressure: This happens when the pressure in the non-potable system exceeds the pressure in the potable water supply. Contributing factors include:
- Elevated storage tanks
- Booster pumps
- Thermal expansion
- Interconnected piping systems with different pressure zones
According to the American Backflow Prevention Association Report, hundreds of documented backflow incidents across the U.S. have led to serious contamination events, emphasizing the ongoing need for strict cross-connection control and backflow prevention enforcement.
Types of Backflow Preventers
Backflow prevention systems range from simple mechanical devices to complex assemblies with multiple safety features. The selection depends on the hazard level and specific application requirements.
Atmospheric Vacuum Breakers (AVB)
These basic devices protect against back siphonage in low-hazard applications.
The AVB operates through a simple float and spring mechanism that opens to the atmosphere when system pressure drops, preventing vacuum formation.
Applications: Irrigation systems, laboratory faucets, and residential hose connections
Limitations: Cannot withstand continuous pressure and offers no protection against backpressure
Pressure Vacuum Breaker (PVB)
The PVB assembly combines a spring-loaded check valve with an atmospheric vent, providing enhanced protection compared to AVBs.
These devices include shutoff valves and test cocks for field testing capabilities.
Key Features:
- Spring-loaded air inlet valve
- Check valve mechanism
- Two shutoff valves
- Two test cocks for field testing
PVB assemblies protect against both low and high hazards under back-siphonage conditions but cannot handle back-pressure situations.
Double Check Valve Assembly (DCVA)
The DCVA represents the most common backflow preventer for fire protection systems.
This assembly incorporates two independently operating spring-loaded check valves in series, providing redundant protection.
Components:
- Inlet shutoff valve
- Two spring-loaded check valves
- Four test cocks
- Outlet shutoff valve
The double-check valve assembly operates on the principle of redundancy—if one check valve fails, the second valve maintains protection.
This design provides reliable protection against low-hazard cross-connections under both back siphonage and backpressure conditions.
Reduced Pressure Zone Assembly (RPZA)
The RPZA offers the highest level of protection through its sophisticated design incorporating a hydraulically operated relief valve.
This assembly creates a zone of reduced pressure between two check valves, making it virtually fail-safe.
Advanced Features:
- Two independently operating check valves
- Differential pressure relief valve
- Continuous monitoring capability
- Field testing provisions
The relief valve opens when either the check valve leaks or when backflow conditions occur, discharging water to the atmosphere and maintaining system integrity.
This design makes RPZA assemblies suitable for high-hazard applications where maximum protection is required.
Double Check Detector Assembly (DCDA)
This specialized assembly combines the protection of a double-check valve with water usage monitoring capabilities.
The DCDA includes a bypass line with a water meter and a smaller protection device for detecting unauthorized water use.
Spill Resistant Vacuum Breaker (SRVB)
Designed for chemical applications, the SRVB prevents spillage during backflow events while maintaining atmospheric protection.
These devices are commonly used in laboratory and industrial settings where chemical contamination poses significant risks.
How Backflow Preventers Work
Backflow prevention systems operate on fundamental hydraulic principles, utilizing pressure differentials and mechanical components to maintain unidirectional flow.
Check Valve Operation
Check valves form the foundation of most backflow prevention assemblies. These spring-loaded devices open when forward pressure exceeds the spring tension and close automatically when flow reverses or stops.
The spring tension is calibrated to specific pressure differentials, typically ranging from 1 to 5 PSI, depending on the application.
This precise calibration ensures reliable operation while minimizing pressure loss during normal flow conditions.
Reduced Pressure Zone Principles
RPZA assemblies create a hydraulically maintained air gap through their relief valve mechanism.
During normal operation, the pressure in the zone between check valves remains lower than both upstream and downstream pressures.
When backflow conditions develop, the relief valve opens, discharging water and maintaining the pressure differential.
This action prevents contaminated water from reaching the potable supply regardless of the check valve condition.
Testing and Monitoring Systems
Modern backflow prevention assemblies include integrated testing capabilities through strategically placed test cocks.
These ports allow certified technicians to measure pressure differentials and verify proper operation without disassembling the device.
Advanced installations may incorporate electronic monitoring systems that provide real-time status information and automated alerts for maintenance requirements.
Installation Requirements and Best Practices
Proper installation ensures optimal performance and regulatory compliance of backflow prevention systems. Installation requirements vary based on local codes and specific application needs.
Sizing Considerations
Backflow preventer sizing must account for system flow requirements and pressure loss characteristics.
Most assemblies create pressure drops ranging from 5 to 15 PSI, which can significantly impact system performance if not properly considered during design.
Professional engineers should conduct hydraulic calculations to determine appropriate sizing, considering peak flow demands and available supply pressure.
Location and Accessibility
Backflow preventers require accessible locations for testing and maintenance activities. Installation guidelines typically specify:
- Minimum clearances around assemblies
- Protection from freezing conditions
- Adequate drainage for the relief valve discharge
- Security measures to prevent tampering
Drainage Requirements
RPZA assemblies require proper drainage systems to handle relief valve discharge. Inadequate drainage can cause flooding and property damage during backflow events or routine testing procedures.
Drainage systems should be sized to handle the full flow capacity of the relief valve and directed to appropriate disposal locations.
In areas subject to freezing, drainage lines require insulation or heating systems to prevent ice blockage.
Regulatory Requirements and Code Compliance
Backflow prevention requirements stem from local water authorities and plumbing codes rather than fire protection standards.
The Uniform Plumbing Code (UPC) provides model requirements adopted by many jurisdictions.
UPC Requirements
The 2018 UPC mandates backflow prevention for fire protection systems based on hazard classification and system characteristics:
Standard Requirements: Fire protection systems normally under pressure require protection by approved backflow prevention assemblies, with exceptions for residential systems using potable water piping materials.
High-Hazard Applications: Systems containing antifreeze, corrosion inhibitors, or other chemicals require reduced-pressure zone assemblies for maximum protection.
Fire Department Connections: Systems with fire department connections located within 1,700 feet of non-potable water sources require enhanced protection due to potential contamination during firefighting operations.
Testing and Certification Requirements
Most jurisdictions require annual testing of backflow prevention assemblies by certified technicians.
Testing protocols verify the proper operation of all components and document compliance with performance standards.
According to the American Water Works Association (AWWA Manual M14), most testable backflow preventers need some form of maintenance or adjustment during annual inspections, reinforcing the importance of regular inspection programs.
Applications in Building Systems
Backflow prevention requirements apply to various building systems where cross-connections exist between potable and non-potable water supplies.
Fire Protection Systems
Fire sprinkler and standpipe systems represent the most common application for backflow preventers in commercial buildings. These systems contain stagnant water that can develop bacteria and other contaminants over time.
System-specific considerations include:
- Pressure loss impacts on hydraulic calculations
- Relief valve discharge accommodation
- Integration with fire department connections
- Seismic bracing requirements
HVAC Systems
Heating and cooling systems may require backflow protection when connected to potable water supplies. Applications include:
- Boiler makeup water systems
- Cooling tower connections
- Humidification systems
- Heat exchanger supplies
Industrial Applications
Manufacturing and processing facilities often require specialized backflow prevention due to chemical processes and non-standard water uses. Risk assessment helps determine appropriate protection levels.
Common industrial applications include:
- Process water systems
- Cleaning and sanitizing operations
- Chemical mixing stations
- Laboratory water supplies
Conclusion
Backflow preventers are essential components in modern plumbing and water systems, acting as the first line of defense against contamination.
By understanding how these devices function, the risks they mitigate, and the importance of proper installation and maintenance, building professionals and property owners can ensure long-term water safety and regulatory compliance.
As infrastructure ages and system demands increase, investing in effective backflow preventer design and routine testing is more critical than ever.
Contact us today to learn more about our backflow preventer design services.
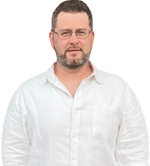
Keith Fink
Keith is the Franchise Brand Manager at NY Engineers, Keith is all things related to our project portfolio, brands and all things you need to know before we start your project.
Join 15,000+ Fellow Architects and Contractors
Get expert engineering tips straight to your inbox. Subscribe to the NY Engineers Blog below.