Our Compressed Air Systems Solutions
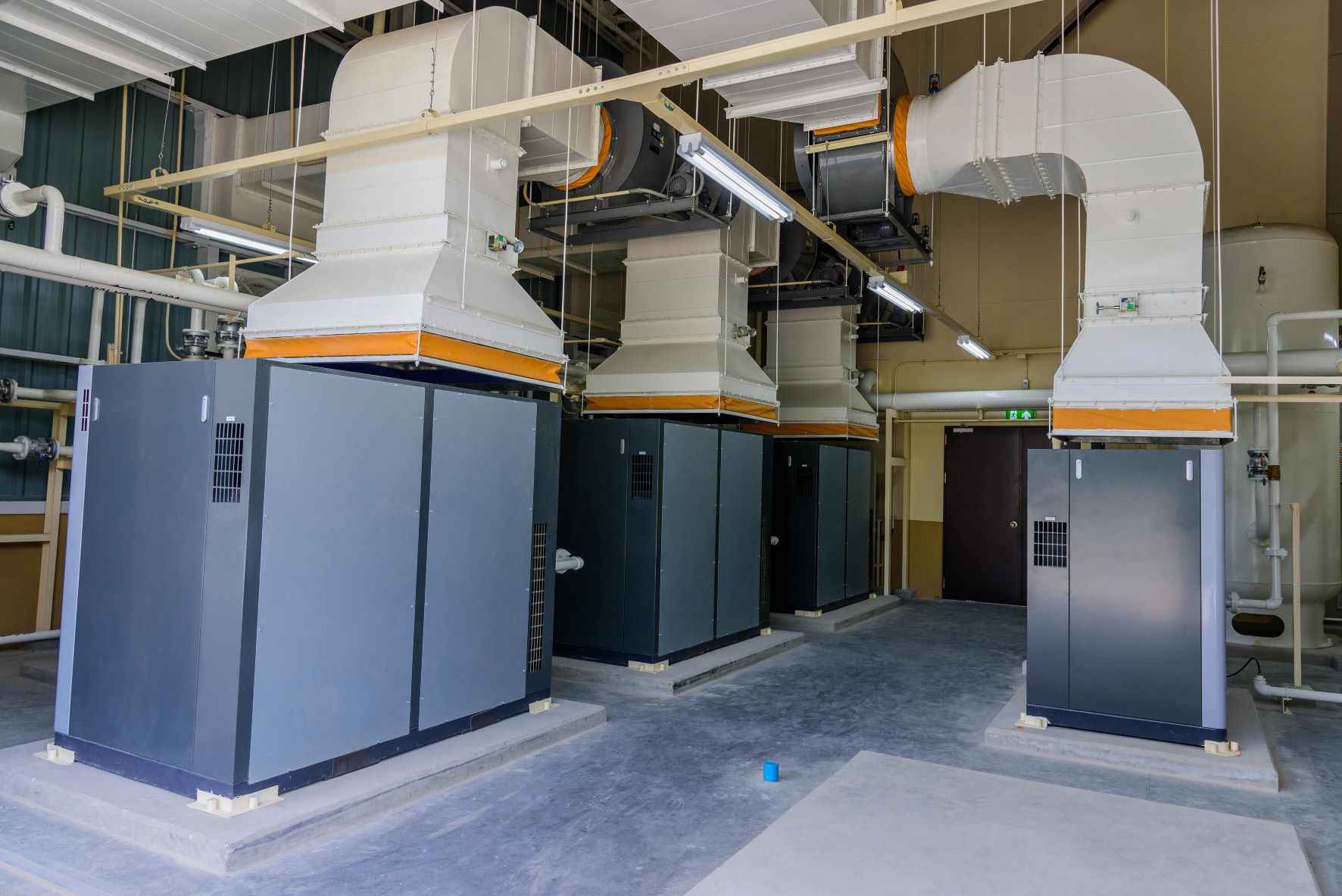
How do NY Engineers help your compressed air systems? Our engineering team will assess air compressor systems to understand their components such as filters, valves, dryers, receivers, and many more. An inspection of these basic components helps us maintain, diagnose, and repair the system.
If not well-maintained, compressed air systems can consume more power and thus cost the homeowner exorbitant energy bills. Also, their repair and replacement costs could be exorbitant if routine maintenance is compromised. Many homeowners overlook this need to maintain the air compressor systems until they are faced with intolerable energy costs.
Maintaining these systems comes at reasonable costs than it would be the case if they were broken, which then prompts repair and replacement costs into the equation.
Our Compressed Air Systems Made Energy Efficient and Affordable
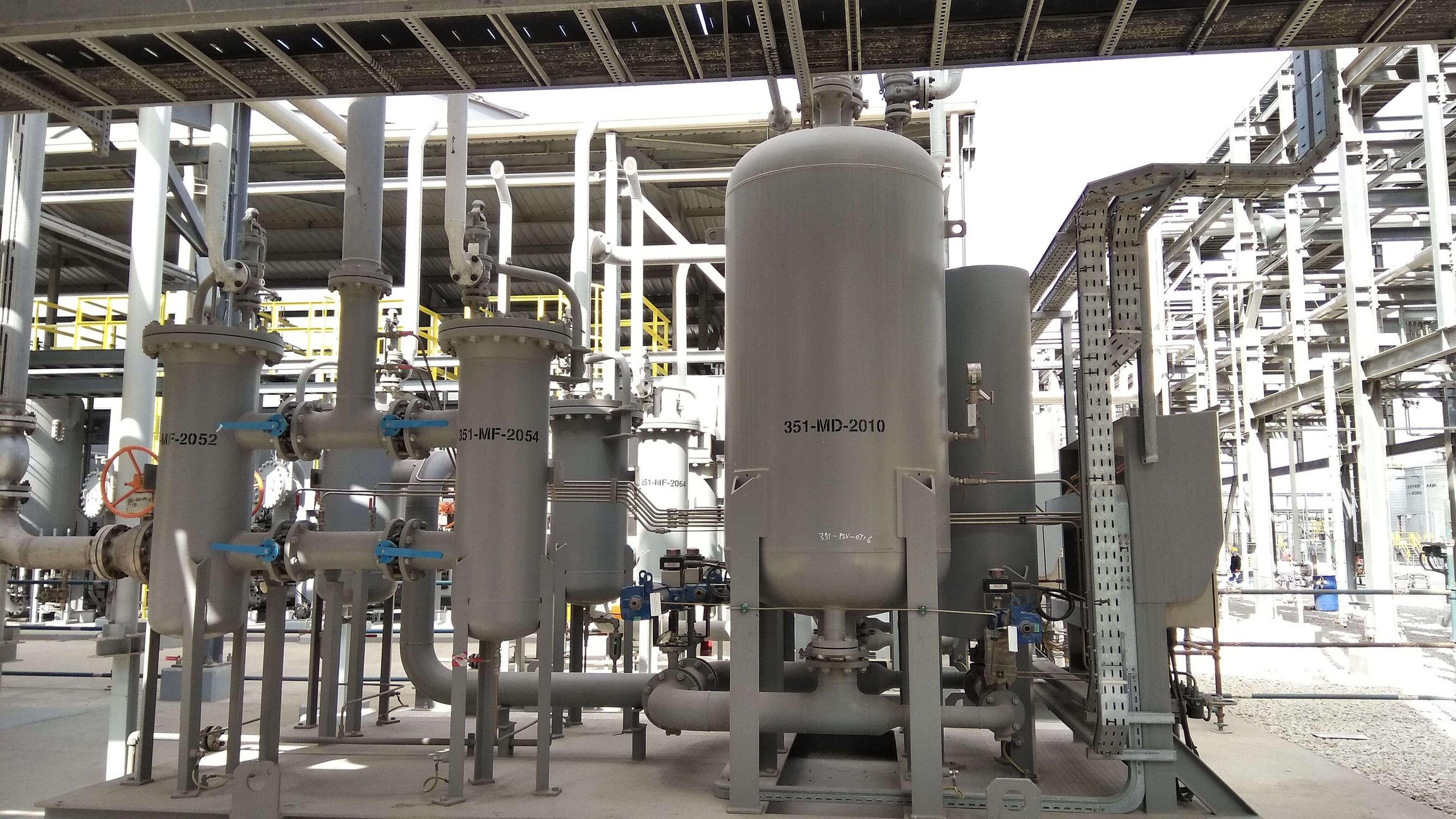
We believe in the provision of best MEP engineering services over price consideration. Many companies prioritize profits whereas we prioritize satisfaction guarantee and customer retention. Our systems are energy-efficient and cost-effective. We do not install the systems and forget about your existence. Our technicians are well-versed with customers services; therefore, they will be with you every step of the way while finding energy-efficient solutions without compromising quality.
Our ability to excel in providing energy-efficient compressed air systems is attributed to our broad knowledge of engineering projects on the market.
How to Ensure that Compressed Air Systems Are Well-Maintained
Air compressor systems have increasingly become popular in many households and businesses in the United States due to their indispensable functions and efficiency in providing clean, cool, and dry air for a variety of commercial and industrial applications. Their popularity can be compared to the usage of water, natural gas, and electricity. However, to function efficiently, they need the power supply and strategic system maintenance.
If not well-maintained, compressed air systems can consume more power and thus cost the homeowner exorbitant energy bills. Also, their repair and replacement costs could be exorbitant if routine maintenance is compromised. Many homeowners overlook this need to maintain the air compressor systems until they are faced with intolerable energy costs.
Maintaining these systems comes at reasonable costs than it would be the case if they were broken, which then prompts repair and replacement costs into the equation. A typical compressed air system contains a number of components as highlighted below, and replacing each could cost a lot. To ensure proper maintenance and installation of compressed air systems, a New York MEP technician should take the full responsibility for the tasks. An inexperienced person may, on the other hand, struggle to decipher the basic path of a compressed air as well as other vital components such as air filters, aftercoolers, moisture dryers, and many more.
Compressed air system components are highlighted below; understanding these components helps one to spot the problem areas to fix so as to avoid impending destructions.
Basic Components of Compressed Air Systems
- Intake filter: an air intake filter is an equipment designed to trap airborne particles such as dust and pollen that could damage the inner components of the compressor. This filter has to be effective to lengthen the durability of the air compressor.
- Compressor: this is the main component that converts power into kinetic energy by compressing the air. There are various models of compressors, viz. centrifugal, rotary screw, and reciprocating. While they differ in the design and air compression path, they achieve the same functionality.
- Aftercooler or intercooler: the intercooler is often involved in multistage air compressors and it comes before the aftercooler. The aftercooler ensures that the discharged air is cooled. The compressed air systems need a lubricant, and this lubricant can be deprived of its lubricant characteristics by extremely hot air if not cooled, hence the indispensability of the aftercooler.
- Receivers: receivers provide a temporary storage of air before it is routed to the equipment that needs a compressed air. Along the route, there are controls to reduce the pressure rate ꟷ measured in psi ꟷ to the required measurement.
- Dryers: the compressed air may contain a high content of moisture, which can damage the components in the system. The dryers are installed to remove the condensation so as to prevent the damages.
These are the basic components of a typical compressed air system. Properly and efficiently maintaining the system can yield optimal productivity results, reduced energy costs, downtime, and reduced repairs.
The complexity of compressed air systems makes it seem challenging for anyone to properly and efficiently maintain them. For this reason, homeowners should consider the services of a qualified and experienced engineer in New York to optimize their air compressor systems.
Maintenance of these systems prevents system’s efficiency drop, air leakage, poor moisture capture, excessive contamination and breakage of other inner components. As a basic guideline, the following should be checked to ensure that these systems are well-maintained:
1. Inspection and maintenance of filters
Filters mainly filter the airborne particles and let only air to pass through. Because of this functionality, they will eventually get clogged and thus drop the inflow of air pressure and eventually the overall system performance. That being said, they have to be cleaned to remove the dirt. If the entire system drops in performance on account of dirty filters, the homeowner may suffer massive energy bills.
2. Lubricate the motors
To function efficiently, the components of the compressed air systems need a lubricant. It will help reduce friction between the components and then prevent a rapid wear. Oftentimes, a reduction in oil or its lubricant properties is caused by a failure of aftercoolers which then leads to overheating. The aftercoolers and the oil should be inspected and then fixed.
3. Inspect the drain traps
The drain traps ensure that particulates are trapped accordingly for a clean and dry air. If they are malfunctioning, the quality of air could be compromised.
4. Inspect and fix air leakage
Any leakage could signal an underlying problem within the system; energy might, therefore, be wasted while the compressed air system is not yielding optimal results. A quarter-inch of leakage at 100 psi can cost the homeowner over $2500 in a year. The air leaks can also be attributed to a failure of the air filters; for instance, particles may have clogged the pipes and therefore led to corrosion which resulted in air leakage. A technician can unfold the base cause of any air leakage in this complex system.
5. Adhere to routine maintenance
This is perhaps the single most important point in here. If the system is consistently maintained as per the routine recommended by the manufacturer, the aforementioned issues will be spotted and then fixed accordingly. There will not be any air-filter issues, air leakage, poor moisture control or any other related problem with the compressed air systems.
A routine maintenance could be scheduled monthly, quarterly, semi-annually or annually according to the manufacturer. If the system is used heavily, one should consider scheduling the routine maintenance at least monthly or quarterly.
6. Turn the system off if not in use
Not only will you be saving the energy costs by turning the machine off, but also reducing a normal wear of the components. Maintenance costs will also be saved significantly when the air compressor system is turned off if not in use.
Conclusion
Compressor air systems are used frequently in commercial and industrial applications. For this reason, they need to be well-maintained to retain their optimal performance. These systems are characterized by a number of components such as air filters, aftercoolers, air-oil separators, dryers, and valves. Their components could wear over time, and so they need a routine maintenance.
Hire a qualified MEP technician to maintain or install your air compressor systems.
Because air compressor systems are complex engineering machines, they need highly technical and experienced engineers to perform this maintenance. Even the installation part requires engineers to optimize their design and save you costs.