Common Mistakes to Avoid that Wasting the Capital of Building Owners
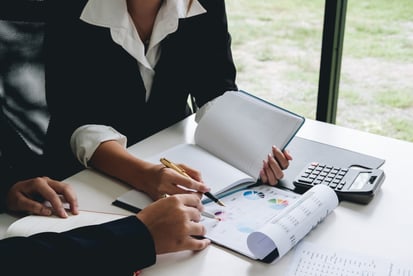
The cost of developing and managing a building is high, especially in places like New York City. However, there are many ways in which property owners can avoid spending more than necessary. Design decisions have an impact throughout the entire building life cycle, and costs can be optimized with well-planned maintenance and eventual building upgrades.
Residential and commercial developers can become more competitive if they lower the total ownership cost of buildings. This increases profit margins, and part of the savings can be transferred to tenants, offering lower rental rates than competitors.
This article describes some common mistakes that increase the ownership cost of buildings, without offering anything in return to project owners.
Optimize your construction costs and achieve long-term savings.
Oversized MEP Installations
For building developers, the “more is better” mindset applies for profit margins, occupancy rates and return on investment. However, this does not apply for the capacity of building systems; for instance, a 300-ton chiller plant provides no benefit if the maximum cooling load is 200 tons.
- Oversized equipment has a higher price and a higher operating cost.
- Maintenance is more demanding when building installations are oversized, and part replacements are more expensive.
- In some cases, building performance suffers with oversized equipment. For example, an HVAC system that produces excessive heating or cooling causes discomfort for occupants, and possibly health issues.
- Oversized equipment operates at partial load, and many types of equipment suffer an efficiency drop.
Top performance is achieved when building systems are optimally sized, and a MEP engineering company can select the most suitable equipment capacities. Oversizing is common when MEP installations are sized based on “rules of thumb”, instead of a detailed analysis of building requirements.
Change Orders During Construction
Many projects become more expensive due to changes during their construction process. This often occurs when the project scope is not clearly defined, or when conflicting equipment locations are specified for different building systems. There are many ways to minimize change orders, or prevent them completely:
- Arrange an initial meeting with equipment suppliers and contractors, to ensure there are no conflicting specifications in design documents.
- Work with a single MEP engineering firm, instead of having separate design teams for mechanical, electrical and plumbing systems. When design teams are separated, they have no way to tell if the proposed layout clashes with another building system.
- 3D modeling tools such as Revit are very useful, since they can detect conflicting specifications right away.
Design changes are much simpler and faster than modifications to completed work during the construction phase. Also consider that design changes only require man-hours from the engineering team, while changes during construction waste materials and labor.
Not Upgrading Building Systems
Buildings last for many decades, and this means that MEP systems eventually become outdated, as new technologies reach the market. Developers should get property assessments at regular intervals to find improvement opportunities. For example, fluorescent lighting was an excellent building upgrade when it was a new technology, and now LED lighting is the most cost-effective option.
Building systems wear down with use, gradually increasing the consumption of electricity, gas and water. In addition, these services tend to increase in cost over time. An effective solution is upgrading MEP system when emerging technologies reach the market at a competitive price.
Not Having a Preventive Maintenance Program
Preventive maintenance is much more effective than fixing problems once they occur. When a maintenance team follows a reactive approach, issues are more expensive to fix and more disruptive for the building. Major equipment breakdowns can also damage other components, leading to reparations that would not have been necessary with preventive maintenance.
Also consider that preventive maintenance can be scheduled, while emergency reparations cannot. This means that parts can be purchased in advance with a preventive maintenance program, while emergency reparations require emergency purchases, and the availability of components is not guaranteed.
Conclusion
Building ownership costs can be reduced in many ways. Professional design services, effective project management, frequent property assessments and a preventive maintenance program can all save thousands of dollars each year. While these services require skilled labor, their cost is only a small fraction of the savings achieved - they can be considered a lucrative investment.
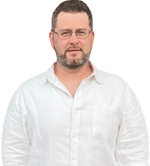
Keith Fink
Keith is the Franchise Brand Manager at NY Engineers, Keith is all things related to our project portfolio, brands and all things you need to know before we start your project.
Join 15,000+ Fellow Architects and Contractors
Get expert engineering tips straight to your inbox. Subscribe to the NY Engineers Blog below.