How Do MEP Engineers Estimate Project Costs?
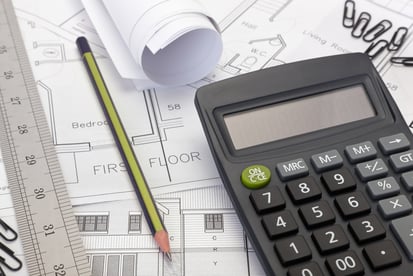
Project cost estimation is a very important element of construction management. Before a building starts construction, developers and contractors must have a cost baseline that can be used to compare the real costs of completed work. With a detailed cost estimation, project managers can monitor ongoing work to ensure it stays under budget.
To deliver an accurate cost estimate, MEP engineers must first know exactly what is being built. Therefore, cost estimation is normally carried out at the end of the design phase. While a broad estimate is possible before having a completed design, a detailed calculation requires project drawings and specifications.
Consider that project cost estimates are time-sensitive, since industry conditions are always changing. For example, if a real estate developer has the cost estimate for a building that was completed 5 years ago, it will no longer apply for an identical construction today. Material and labor costs normally increase over time, and there are also some technologies that become more affordable. Regulatory conditions may have also changed - import taxes have a significant impact on material costs, for instance.
The Project Cost Estimation Process
To reach a project cost estimate, MEP engineers must first know the scope of work. Using the scope as a starting point, the traditional approach to reach a cost estimate is the following:
-
The project scope is broken down by areas, such as mechanical, electrical and plumbing. In project management, this is called a Work Breakdown Structure (WBS).
-
Each building system is further divided into cost items, with measurable quantities of materials and labor. Many tasks in construction also include equipment costs.
-
Based on local prices, MEP engineers can assign a unit cost to each item.
-
Each unit price is multiplied by the corresponding quantity of work, and the sum of all items yields the cost estimate for the project.
While the basic procedure for cost estimation is simple, it can consume plenty of time, especially in large projects. Modern engineering firms use powerful tools that simplify drafting and cost estimation, and MEP engineers can focus on making the best technical decisions.
Building Information Modeling (BIM) is a design tool that greatly simplifies the cost estimation procedure. MEP engineers can create a digital model of all building systems, and then assign material properties to components. Material take off can require several days with a manual procedure, but modern software can perform calculations within seconds.
Consider that project cost estimation requires technical knowledge and experience, even with modern design tools. There is a common misconception that advanced software displaces engineering services, but software only provides useful results if the inputs and design parameters are correct. Most projects also involve decisions between different types of equipment or system layouts, and only qualified engineers can choose an optimal configuration.
Project Cost Optimization: Going One Step Further
When you work with the best MEP engineers, they go beyond a simple cost estimate, proposing ways to reach the same final result with lower costs. For example, many buildings have oversized installations that are more expensive and more demanding in maintenance; a qualified MEP engineering firm will make sure you install the optimal capacity for your building.
Get a detailed design and cost estimate for your building project.
MEP engineers may also suggest modifications that increase some upfront costs, but offering long-term savings that are much higher. LED lighting is a good example: it is slightly more expensive than conventional lamps and luminaires, but it reduces lighting expenses by over 70% in some cases.
While the project cost estimate is important, developers should also consider the total cost of ownership over the building’s service life. Cost savings can often be achieved without sacrificing performance, and some projects can achieve lower cost and higher performance at once with smart decisions. On the other hand, cost savings at the expense of performance should be avoided, since extra costs in the long run may be several times higher than the initial savings.
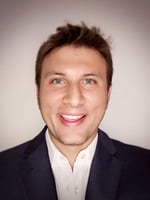
Michael Tobias
Michael Tobias, the Founding Principal of NY Engineers, currently leads a team of 150+ MEP/FP engineers and has led over 4,000 projects in the US
Join 15,000+ Fellow Architects and Contractors
Get expert engineering tips straight to your inbox. Subscribe to the NY Engineers Blog below.