Upgrading Aging Mechanical Equipment in NYC
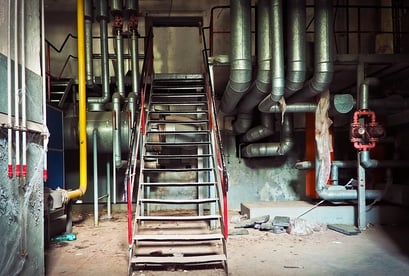
Most of the energy consumption in NYC buildings can be attributed to mechanical equipment, especially air conditioning and heating systems. Deteriorated HVAC installations consume more energy than necessary, and can also lead to air quality issues such as excessive moisture and mold growth.
Although mechanical equipment upgrades for residential and commercial properties can represent a significant investment, in the long term it can be more expensive to sustain the operation of aging equipment. A mechanical equipment upgrade is also welcome if the existing HVAC system is no longer able to deliver adequate temperature and air quality conditions.
This article will provide an overview of some cases where a mechanical equipment upgrade makes sense, as well as recommendations to maximize your return on investment.
Upgrading Mechanical Equipment to Save Energy
There are two main reasons why dated mechanical equipment wastes energy: its performance drops due to the deterioration of internal components, and in some cases the technology itself is inefficient even if kept under optimal conditions. For example, window-type air conditioners consume much more energy than modern ductless systems, even if the units being compared are new and with the same nameplate capacity.
A direct mechanical equipment upgrade may not be the most cost-effective way to reduce energy consumption if the main cause is found elsewhere. Before proceeding with an HVAC upgrade, it is important to answer two key questions:
- Are energy expenses really caused by poor HVAC performance? There may be other causes such as a deficient building envelope or lack of control over operating schedules.
- Is the original installed capacity adequate? Maybe the original mechanical equipment was oversized or undersized, and the upgrade represents an opportunity to specify the proper capacity, in addition to improving energy efficiency.
You can get in touch with a qualified engineering firm to carry out energy modeling for your facility, and get a precise snapshot of building envelope performance and other conditions that affect energy consumption. If your building envelope is deficient, a mechanical equipment upgrade can still be a good decision, but there many advantages if insulation and airtightness issues are addressed first:
- After improving the building envelope, the new equipment can be specified both smaller and more efficient. Since the installed capacity is less, both the upfront cost and the running expenses are reduced with respect to the baseline scenario.
- A building envelope upgrade improves indoor air quality. Air leaks are eliminated, and the ventilation system can achieve greater control over air supply and exhaust.
It is important to note that any mechanical equipment upgrades must meet the latest version of the NYC Energy Conservation Code, and system commissioning is mandatory in commercial buildings if cooling capacity is at least 480,000 BTU/hour (40 tons), or combined space and water heating capacity is at least 600,000 BTU/hour (50 tons). The following options generally offer the highest energy efficiency among HVAC options.
Function |
Recommended Equipment |
Heating |
Gas-fired boiler with a high Annual Fuel Utilization Efficiency (AFUE) |
Air Conditioning |
Water-cooled chiller with variable-speed compressor |
Heating & Cooling |
Variable refrigerant flow (VRF) system |
There are cases where purchasing the most efficient HVAC equipment available is actually less expensive that going for low- or mid-tier units. Efficient equipment is often eligible for cash rebates from utility companies, reducing the upfront cost and improving the financial attractiveness of the project.
Automatic controls are an excellent complement for any mechanical equipment upgrade, since they ensure the new units only run for as long as necessary, and at reduced output if their full capacity is not needed. Running an HVAC system a partial load generally consumes much less energy than cycling it on and off repeatedly, and component wear is minimized, extending service life and reducing maintenance expenses.
Improving Temperature Control and Air Quality
Old mechanical equipment may no longer be able to meet the heating or cooling load it was designed for due to extensive wear, and the cost of restoring it can be very high. In addition, it may be impossible to meet current building codes with the original equipment regardless of how much it is restored. Keep in mind that old HVAC systems were not capable of part-load operation, and would meet reduced heating and cooling loads by cycling on and off - this is inefficient in terms of energy consumption and detrimental for the service life of equipment. Temperatures also tend to fluctuate above and below the target value, without ever stabilizing.
In the case of heating, oversized equipment is common in older buildings, and precise temperature control can be difficult due to excessive capacity and incompatibility with modern control systems. The blowers on these units also tend to be oversized, which creates a drafty and uncomfortable indoor environment. 20th-century building codes required heating systems to be designed for when the building had its windows open, which results in overheating once insulation and air-tightness are improved.
Upgrades to the ventilation system can improve indoor air quality while reducing energy consumption. For example, a legacy ventilation system with ON/OFF controls can be replaced with a demand-controlled ventilation system, where the fans use high-efficiency NEMA Premium motors and variable-frequency drives for speed control. Keep in mind that reducing the duty cycle of a fan provides linear savings, but reducing its speed reduces power consumption exponentially by a factor of 3; a fan at 50% duty cycle consumes half of the energy compared to another one that runs 100% of the time, but a fan at 50% speed only consumes 12.5% of the energy (50% x 50% x 50%).
Conclusion
In residential and commercial buildings with old HVAC systems, there is an excellent chance to improve three aspects at once: temperature control, indoor air quality and energy efficiency. The first two are beneficial for human comfort, and productivity in the case of commercial buildings. Energy efficiency is always welcome, allowing building systems to deliver the expected performance at a lower cost.
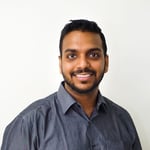
Anuj Srivastava
Anuj Srivastava is a principal partner at NY Engineers. He is known for his MEP franchise market knowledge. Anuj is currently leading a team of 100+ MEP/FP engineers and has successfully led over 1500 franchise projects in the US.
Join 15,000+ Fellow Architects and Contractors
Get expert engineering tips straight to your inbox. Subscribe to the NY Engineers Blog below.