Improving Ventilation Efficiency in NYC Buildings
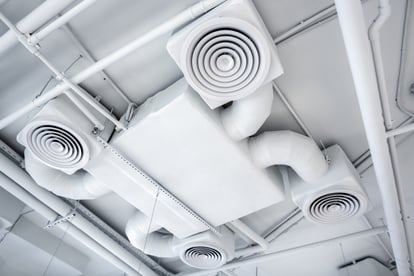
Ventilation systems consume 13% of the energy used in NYC office buildings, which means energy efficiency improvements that target these systems can have a notable effect on the electricity bill. The energy footprint of ventilation is much smaller in residential buildings, accounting for only 1% of energy usage, given that NYC building codes only make mechanical ventilation mandatory in bathrooms and kitchens.
The high energy consumption of ventilation systems in office buildings should come as no surprise, given that modern offices are not normally designed for natural ventilation. In NYC, around 50% of office spaces use air-handling units (AHU), but there are ample opportunities for improvement:
- Only 29% of office spaces in NYC combine an AHU with an economizer, which turns off air conditioning and supplies outdoor air directly when weather conditions are favorable.
- Energy-recovery and heat-recovery ventilation (ERV and HRV) are even more rare, found in only 2% of NYC commercial spaces. ERV systems exchange heat and moisture between the supply and exhaust air, while HRV systems exchange only heat.
What Are the Benefits of Ventilation Improvements in NYC?
The Urban Green Council carried out a study with data from around 15,000 of the largest buildings in NYC, encompassing around 42% of the city’s floor space. They determined that ventilation improvements have the potential to save around 2 trillion BTU of energy per year. In the specific case of office buildings, ventilation upgrades can save around 2,700 BTU/ft2 per year. Of all energy conservation measures, only on-site generation has a higher potential in office buildings, equivalent to 4,100 BTU/ft2 per year.
The payback period of ventilation upgrades in NYC office buildings is around 2 years, making them attractive projects from the financial standpoint. This is equivalent to a yearly return on investment (ROI) of 50%.
Although space and water heating consume much more energy than ventilation in office buildings, upgrades to those systems have a longer payback period than ventilation upgrades. This happens because ventilation consumes electricity, which is expensive in NYC; on the other hand, heating is based mostly on district steam, natural gas and fuel oil, which have a lower cost than electricity. In other words, the return on each dollar spent on efficiency upgrades is higher for ventilation.
In addition to saving energy in office buildings, improved ventilation is beneficial for productivity. This has been verified by Harvard University, the SUNY Upstate Medical University and the Syracuse Center of Excellence after carrying out scientific research on the topic. They determined that an 8% increase in cognitive function, achieved with reduced levels of carbon dioxide and volatile organic compounds, can translate into a yearly economic benefit that ranges from $6,500 to $10,000 per employee. This analysis only considered productivity gains, so the economic benefit is even higher when the health improvements are considered: effective ventilation minimizes infectious disease transmission while reducing the number of sick days per employee. Even in urban settings, indoor air is generally two to five times more polluted than outdoor air, except during high-pollution events such as peak traffic hours.
Improved ventilation also leads to more comfortable office spaces. During a ventilation upgrade, issues such as noise and air drafts can be analyzed and corrected. Noise is detrimental for concentration, and air drafts can affect both concentration and health.
Promising Ventilation Upgrades
Ventilation systems that operate intermittently can reduce their energy consumption significantly if complemented with a variable-frequency drive (VFD). In simple terms, a fan operating at partial speed full-time consumes much less energy than one operating intermittently at full capacity, even if both are supplying the same average airflow. Assume a 5,000-cfm fan will be used for an application requiring 4,000 cfm:
- If the fan operates intermittently 80% of the time to deliver an average airflow of 4,000 cfm, it will consume 80% of the energy needed for full-time operation.
- However, fan speed and power consumption have a cubic relationship. If fan speed is reduced to 80% while the unit remains on, fan power will be reduced to only 51.2%.
It is important to note that the cubic relationship between fan speed and power only applies to open-discharge fans, and savings are reduced when air-handling units must blow air into a pressurized duct. However, reduced speed operation will always have a lower running cost than intermittent operation for a given fan capacity and average airflow.
Variable frequency drives can also be combined with occupancy monitoring to adjust fan output depending on the amount of people present in an office area. This concept is called demand-controlled ventilation and is one of the most efficient ventilation control strategies.
Economizers are another promising upgrade for ventilation systems. Basically, they monitor outdoor air and turn off space cooling systems when the required temperature can be reached with outdoor air alone. It is important to note that economizers do not reduce the energy consumption of fans directly, but they help save on space cooling, an energy expense of the same magnitude as ventilation in office buildings.
Energy recovery systems can also be added to ventilation systems to improve overall HVAC efficiency. Basically, these systems exchange energy between the supply and exhaust airflows to minimize heating, cooling, humidification and dehumidification expenses. A heat recovery ventilation (HRV) system only exchanges heat, while an energy recovery ventilation (ERV) system exchanges both heat and humidity.
- In the cooling season, outdoor air is typically warm and humid. Some of its temperature and humidity are transferred to the exhaust airflow to reduce the load on air conditioning equipment.
- The inverse process is carried out in the heating season, when outdoor air is normally cool and dry. In this case, both heat and humidity are recovered from the exhaust air.
Passive ventilation can achieve significant energy savings in new constructions, if the entire building architecture is designed to take advantage of natural convection. Given that many passive ventilation methods require a specific building architecture, the concept only has limited applications in existing buildings. Building architecture can also be optimized for natural lighting, which is a great complement for passive ventilation; both lighting and heating consume large amounts of electricity in office buildings, respectively 18% and 13% of total energy use.
Conclusion
In terms of financial performance, ventilation system upgrades are among the most promising building upgrades available. These improvements can reduce the energy consumption of not only the system itself, but also that of associated heating and cooling equipment. In addition, improved ventilation can make indoor environments healthier, more comfortable and more productive. Some of the most effective upgrades are variable frequency drives for fan motors, demand-controlled ventilation, economizers and energy-recovery systems.
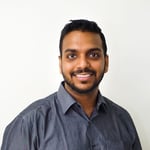
Anuj Srivastava
Anuj Srivastava is a principal partner at NY Engineers. He is known for his MEP franchise market knowledge. Anuj is currently leading a team of 100+ MEP/FP engineers and has successfully led over 1500 franchise projects in the US.
Related Posts
Join 15,000+ Fellow Architects and Contractors
Get expert engineering tips straight to your inbox. Subscribe to the NY Engineers Blog below.